Saito FG73 Umbau
... für eines unserer aktuellen Projekte
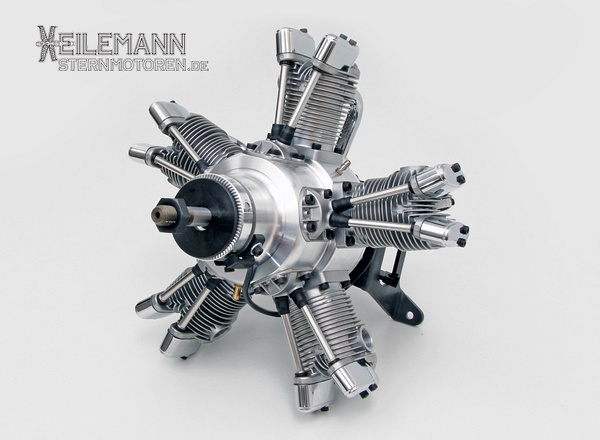
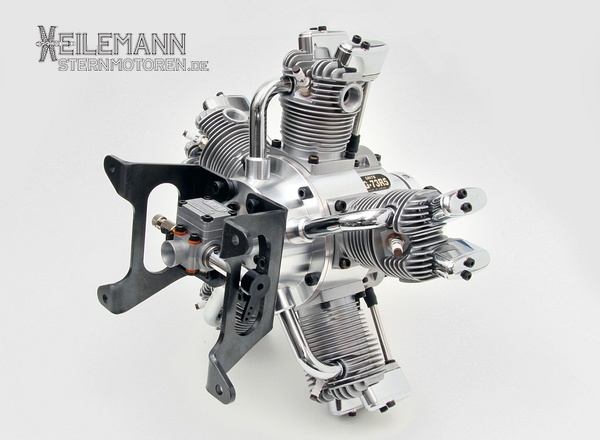
Original Auslieferzustand.
Für unser neues Projekt haben wir uns für einen Saito FG73 entschieden. Er ist perfekt verarbeitet, sieht gut aus und passt im Durchmesser und Gewicht zu unserem neuen Modell. Da unser Modell jedoch eine extrem kurze "Schnauze" hat, mussten wir den mitgelieferten Motorträger ersetzen. Wir fertigten dazu einen neuen Motorträger aus Aluminium an.
Der fertig gedrehte Flansch wurde auf der Fräsmaschine mit Ausfräsungen und Bohrungen weiterbearbeitet.
Die Ausfräsungen dienen zur Luftführung zum Vergaser und ergeben eine Gewichtserleichterung von ca. 50 % zum originalen Motorträger aus Stahl.
Es ist optisch sehr gut gelungen, passgenau und sehr stabil.
Zwischen Zylinder und Motorträger, unter Berücksichtigung der Ansaugrohre, muss jetzt noch der Ringschalldämpfer montiert werden. Leider hatte unser Keleo Ringschalldämpfer, nach dem extrem gekürzten Motorträger, nun keinen Platz mehr.
Also fertigten wir einen neuen Ringschalldämpfer selbst an.
Dafür haben wir uns eine Hilfsvorrichtung angefertigt. Der Ringschalldämpfer wird exakt mittig zentriert um die Position zum Motorträger zu gewährleisten.
Für die Zylinderkopfverschraubungen an den Auslässen haben wir uns Flanschbuchsen mit passenden Überwurfmuttern hergestellt. Die Flanschbuchsen haben wir mit einem Dorn geweitet und die Krümmer eingelötet.
Die Auslasskrümmer haben wir sorgfältig am Ringschalldämpfer eingepasst und hart gelötet.
Der Ringschalldämpfer ist absolut spannungsfrei zu montieren/demontieren.
Jetzt fehlt nur noch das Auslassrohr vom Ringschalldämpfer. Das werden wir dann am Modell seitlich anpassen.
Wir freuen uns darauf weiter zu berichten!
Eine Idee nimmt Formen an
Unser aktuelles Projekt: Der 18 Zylinder Doppelstern mit 700ccm
Seit 2007 fliegen wir nun unseren 9-Zylinder Sternmotor mit 350 ccm in unserer Boeing Stearman PT17. Der Motor ist absolut ausgereift und läuft im harten Alltagseinsatz sehr zuverlässig.
Mario Seidel von Seidel Props brachte uns letzt endlich dazu, das Projekt "18-Zylinder Doppelstern" mit 700 ccm, auf Basis unseres 9-Zylinder Sternmotors, anzugehen. Er hatte die Idee eines 4-Blatt Verstellpropellers, zu dem er einen Motor mit Getriebe benötigte. Nichts besser als unser 18-Zylinder Doppelstern als Versuchsobjekt ist dazu geeignet.
Dieser Bericht ist in mehrere Baufortschritte gegliedert, welche Sie in unserer Timeline oder im linken Menü auswählen können.
Seidel-UMS ST 9-90 Modifikation
Die Vorgeschichte
Friedrich Wolf bat uns die Funktionalität seines neuen SEIDEL UMS ST 9-90 zu überprüfen. Für Friedrich Wolf haben wir schon einen Ringauspuff für den inzwischen historischen ST 5-525 angefertigt. Offensichtlich ist er von unserer Sternmotoren-Kompetenz überzeugt.

Friedrich Wolf hat sich während einer Vorführung von Herrn Seidel auf einem Flugtag in diesen 9-zylindrigen Motor verguckt. Das ist der scalegerechte Motor für eine PZL M-18 Dromader. Durch die Produktion in Indien war der Preis attraktiv. Der Demolauf bei der Motorenübergabe belegte die Funktionalität.

Wir sollten für diesen Motor wieder einen Ringauspuff fertigen. Der kleine Ring den SEIDEL als Zubehör dafür anbietet ist für einen Scalenachbau nicht brauchbar. Außerdem sollten wir Überprüfen warum es nicht möglich ist ein gleichmäßiges Ventilspiel einzustellen. Nach jeder Kurbelwellenumdrehung war die erste Einstellung extrem anders. Auch wurden wir gefragt ob wir denn das hochglänzende Aluminiumgehäuse mit einer „Designed in Germany“ Gravur in eine echte Motorenoptik modifizieren könnten. Den Motor mit Carbonstösselstangen ausstatten und komplett mit unserem Hölzl Glühregler "Star-Glow" verkabeln.
Aber natürlich können wir das!
Das Ventilspiel konnten wir allerdings auch nicht reproduzierbar einstellen. Also machten wir uns auf die Ursachensuche.
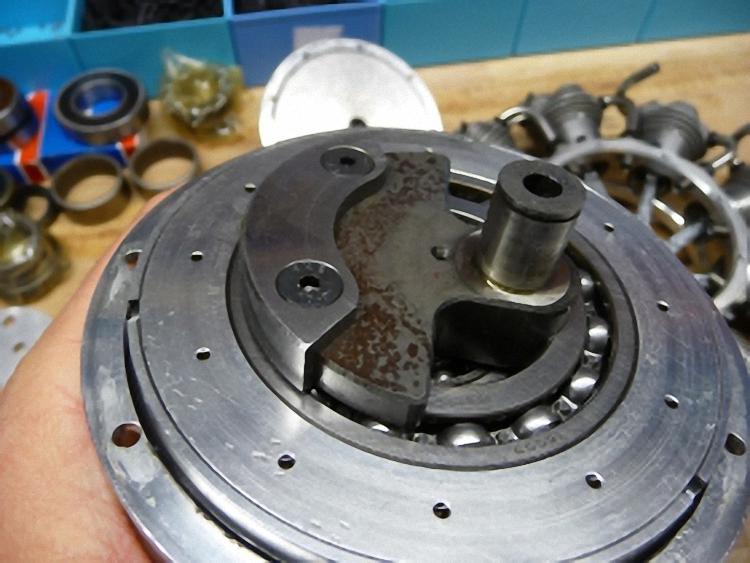
Der zerlegte Motor zeigt eine typische Sternmotorenkonstruktion. Warum einige Teile deutliche Hammerschlagmarkierungen zeigen weiß wohl nur der indische Feinmechaniker.
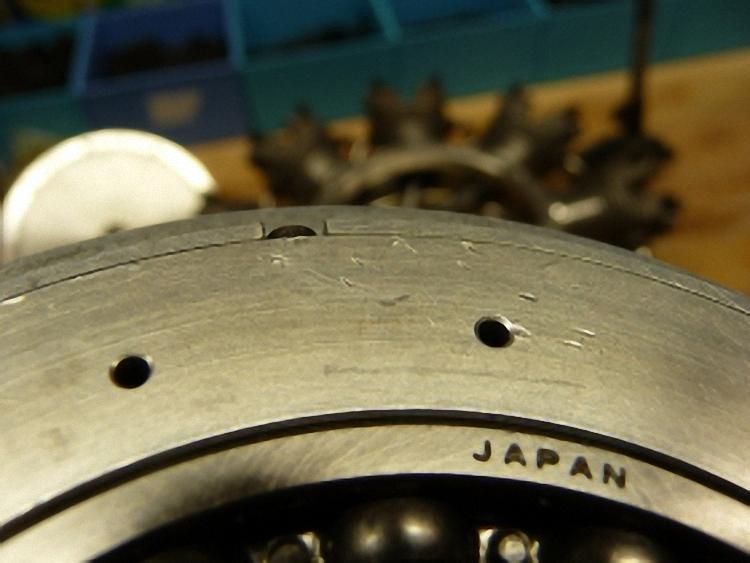
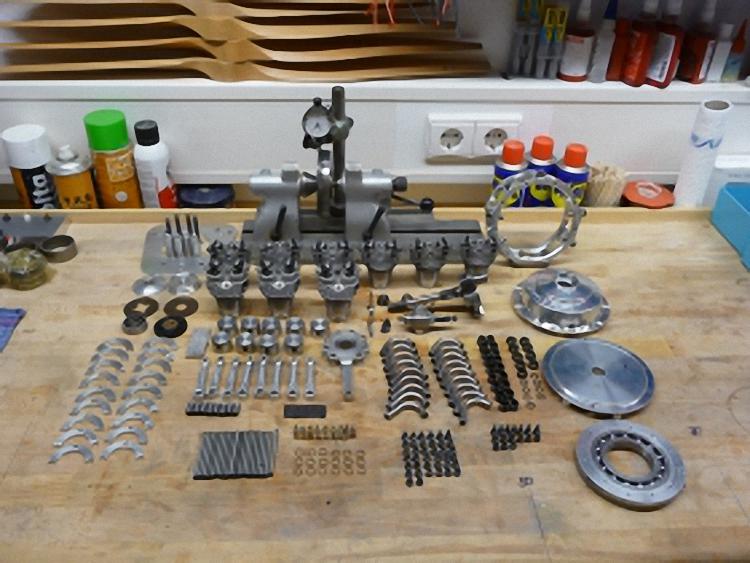
Das Vermessen der Nockenscheibe, die die Ventilstößl antreibt, zeigte Toleranzen von +/- 0.5 mm.
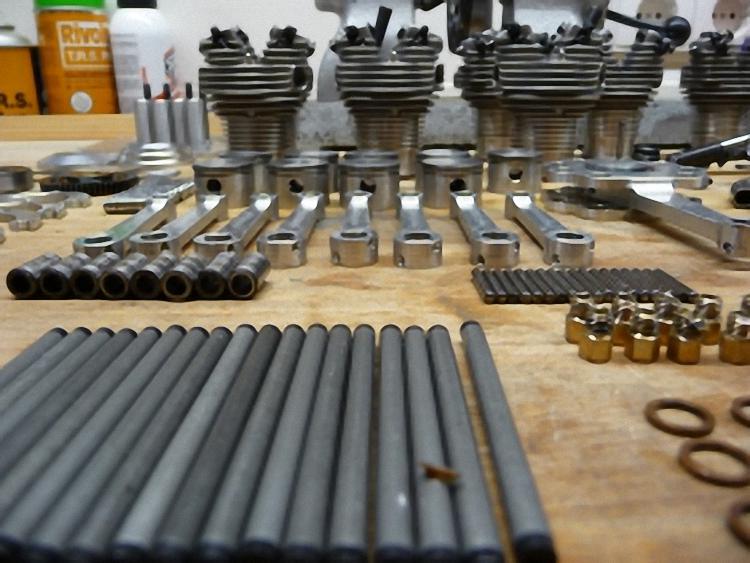
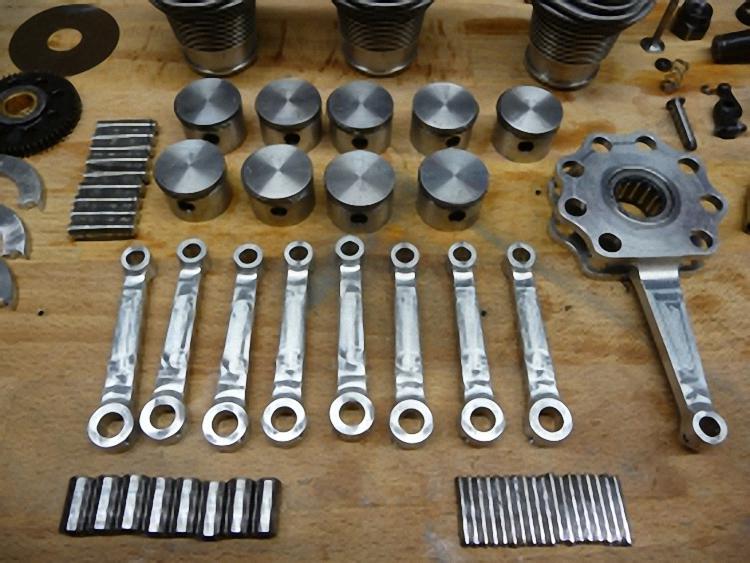
Außerdem ist die Nockenscheibe zweiteilig gefertigt. Wir legen unsere Motoren eigentlich mit weniger Toleranzen aus.
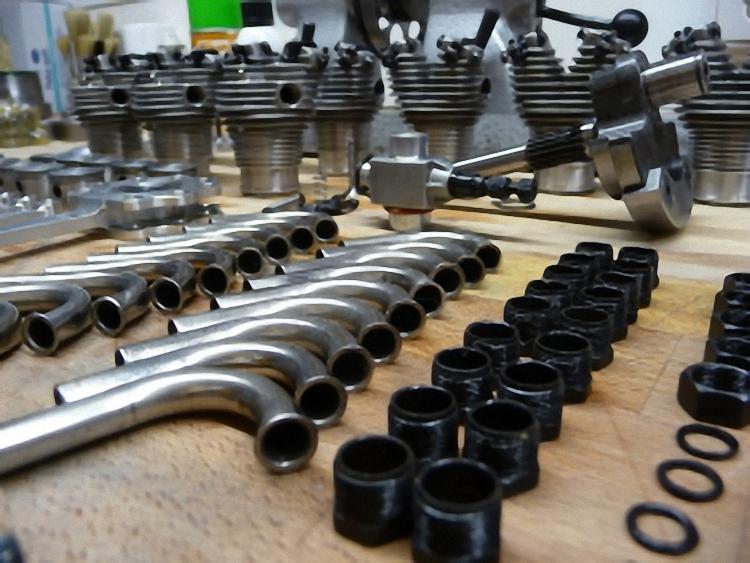
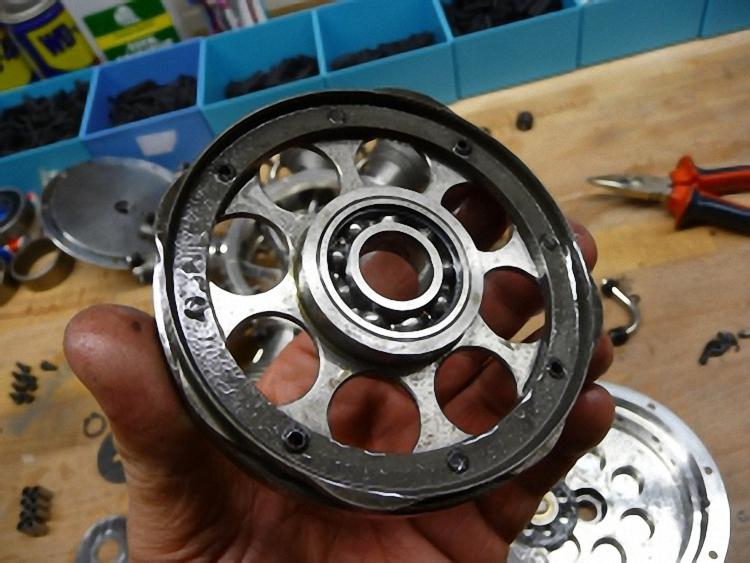
Daraufhin haben wir beschlossen, die Nockenscheibe neu anzufertigen. Wir haben Sie neu dimensioniert: leichter, die Laufbahn ein wenig dicker gestaltet, den Lagersitz dünner, die Steuerzeiten optimiert und alles aus einem Stück gefertigt.

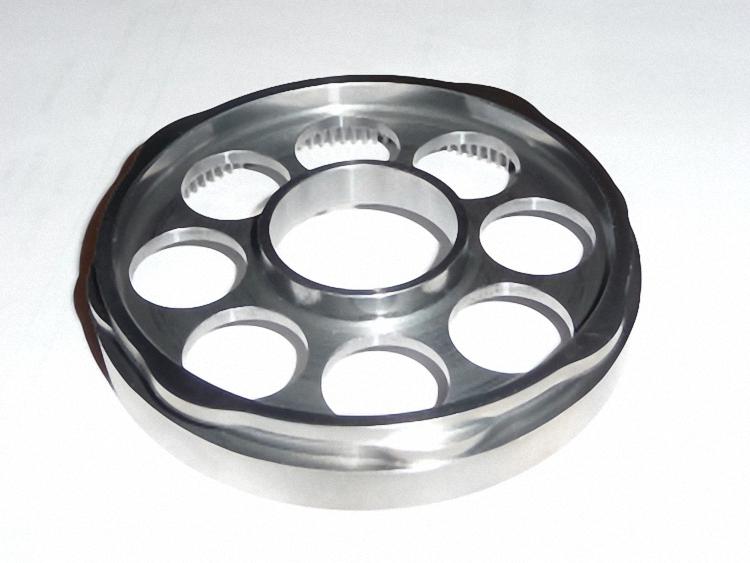
Deutlich zu sehen: dickere Laufbahn für Stoessel, gestoßener Zahnkranz, Nocke an einem Stück gefertigt
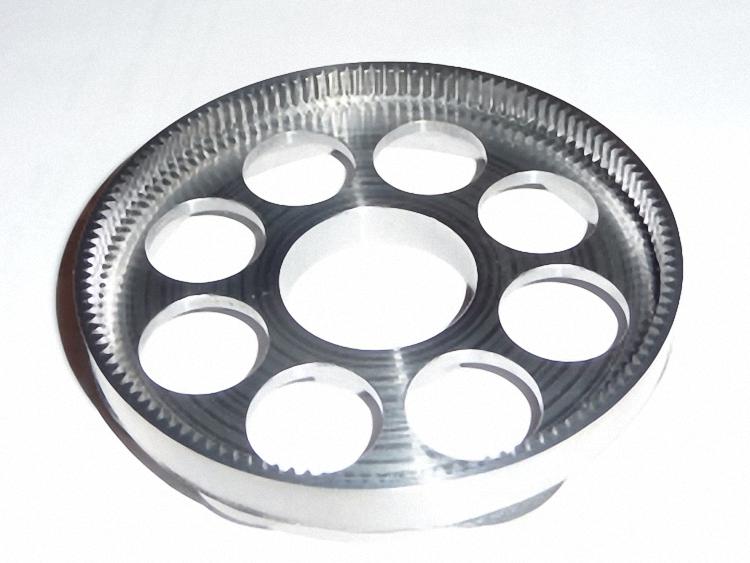
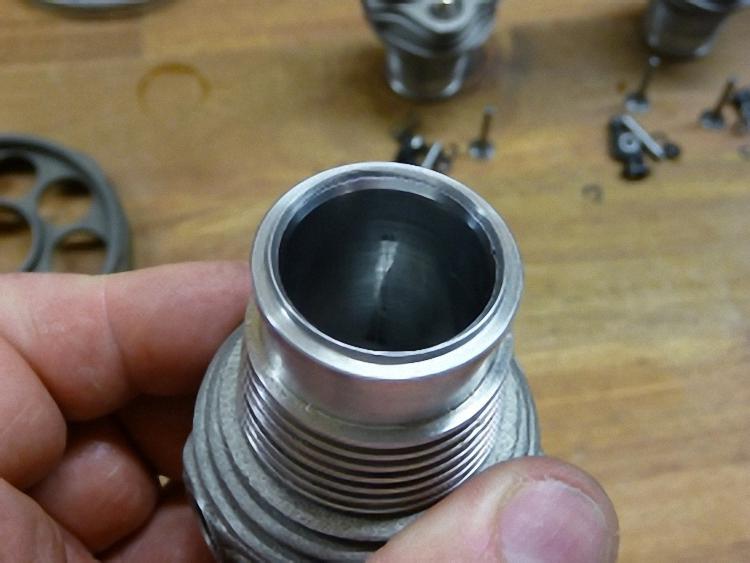
Hier hat der Kolbenring ganze Arbeit geleistet. Da die Zylinderbuchse leicht unrund war, hat er beim ersten Probelauf gleich mal einen Span abgehobelt. Der Zylinder wurde komplett nachgearbeitet.
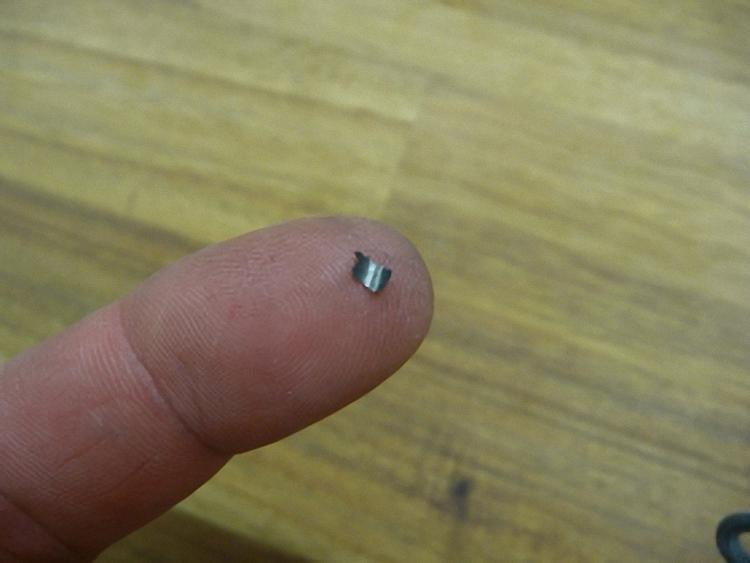
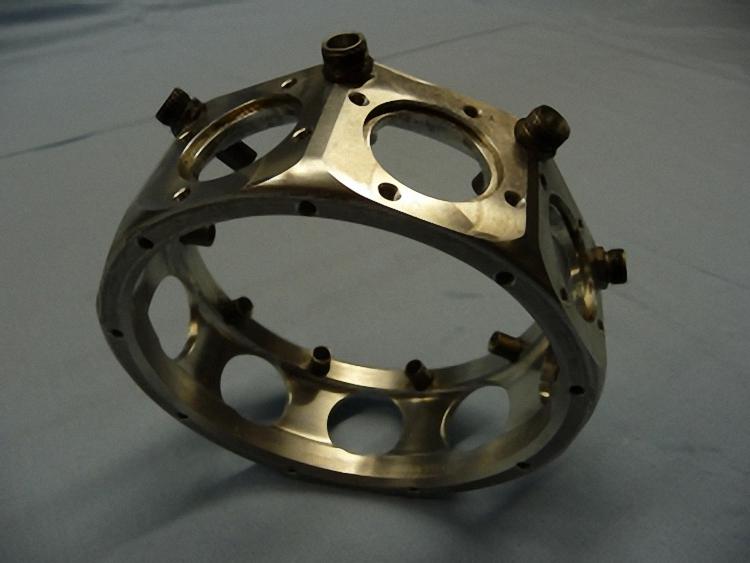
Die originale Oberfläche des Motorgehäuses wurde glasperlengestrahlt und bekam dadurch eine Scale Optik
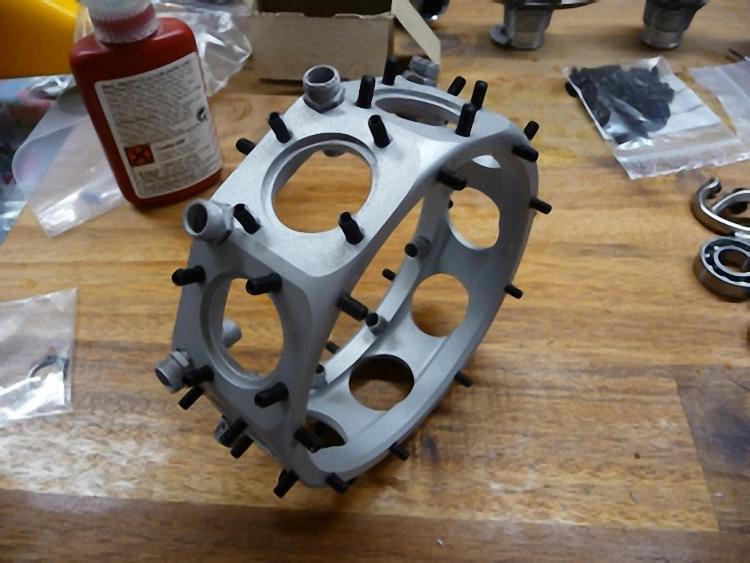
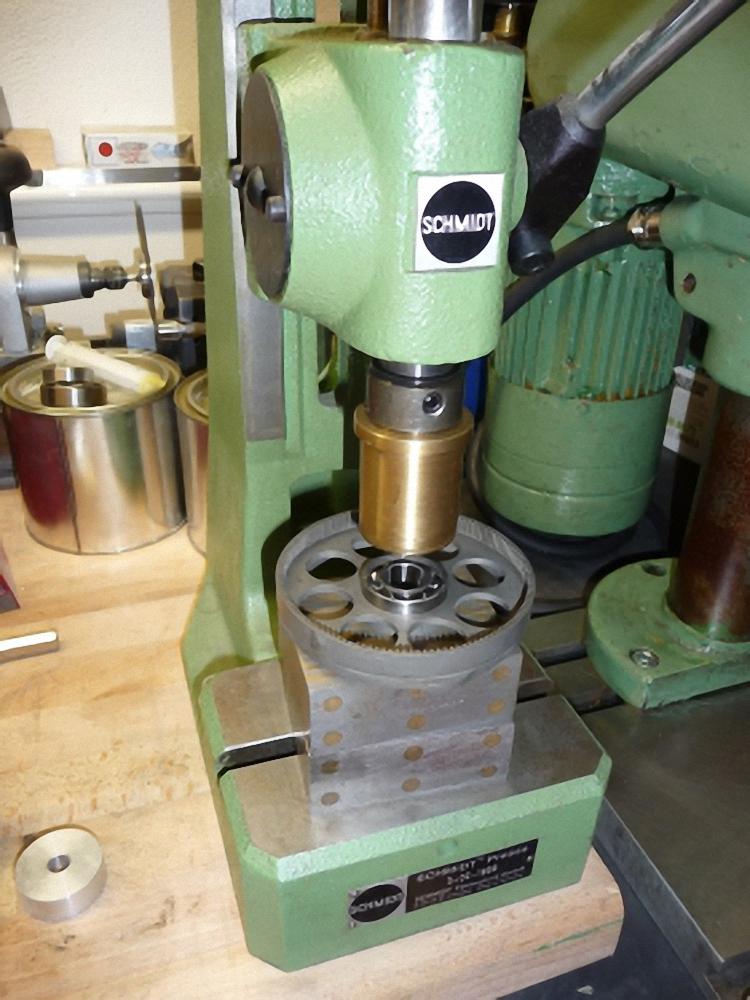
Das vordere Gehäuseteil wurde abgedreht um die unerwünschte Gravur zu entfernen. Alle Gehäuseteile wurden glasperlengestrahlt um eine naturgetreue Oberfläche zu erzeugen. Mit einigen Ölflecken wird diese Oberfläche immer echter. Alle Inbusgehäuseschrauben wurden gegen Stehbolzen und Muttern getauscht.
Wir haben alle standardmäßig verbauten Lager gegen Deutsche Qualitätslager ausgetauscht.

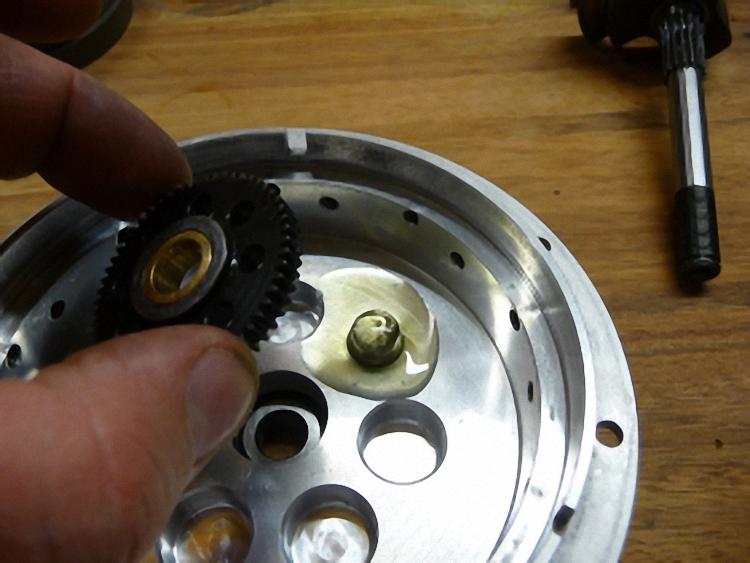
Nun beginnt der Zusammenbau der neuen Nockenscheibe

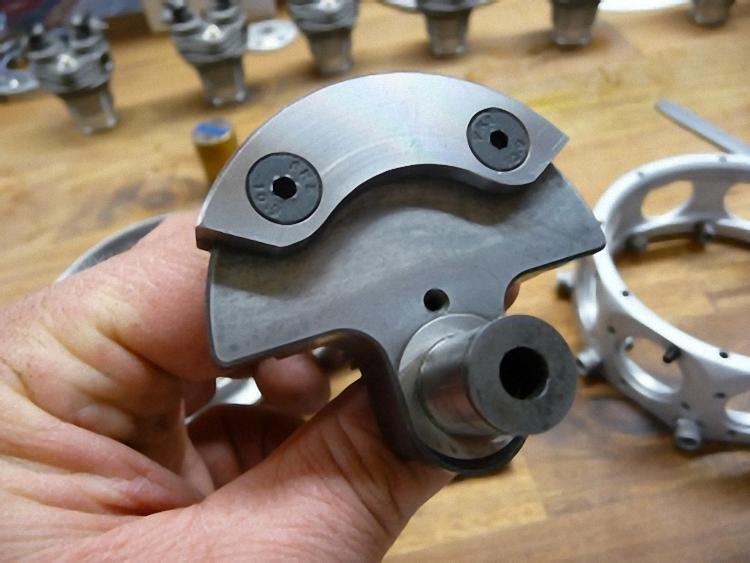
Vom Rost gereinigte Kurbelwelle und Montage der einzelnen Zylinder
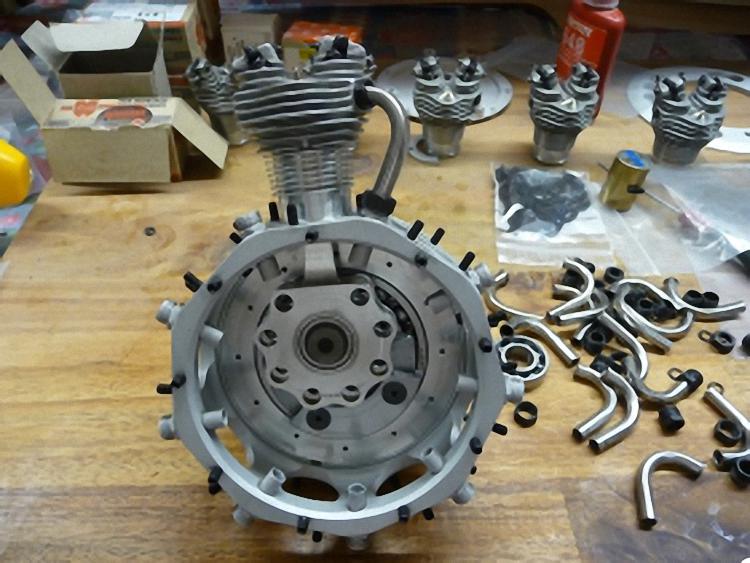
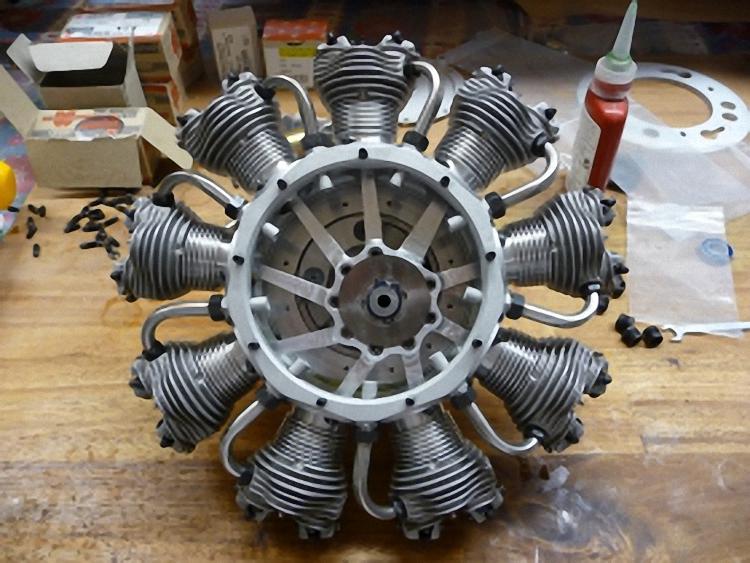
Dann fehlte immer noch der scalegerechte PZL M-18 Auspuffring mit seitlichem Auslass. Rohrbögen im entsprechenden Durchmesser waren nirgends aufzutreiben. Aber wozu sind wir eine Sternmotorenmanufaktur?

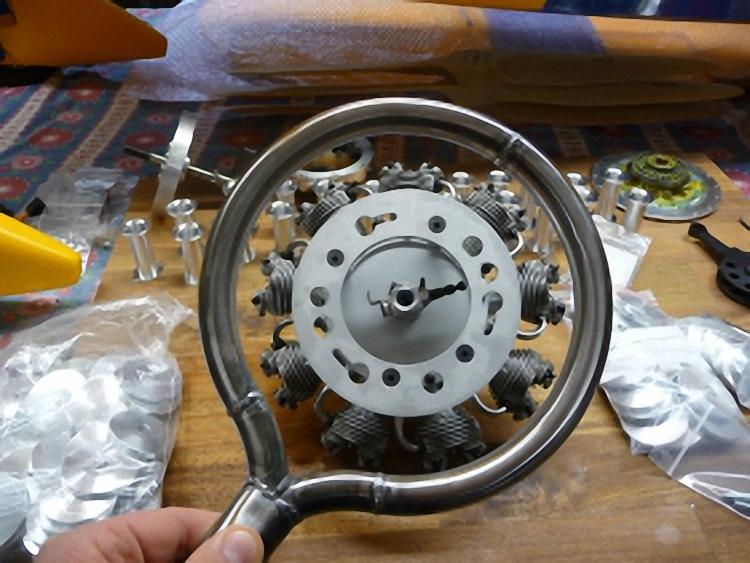
Die spezielle Ringherstellung übernahm KELEO für uns. Die Sonderanfertigung passte sich perfekt hinter den Motorträger ein
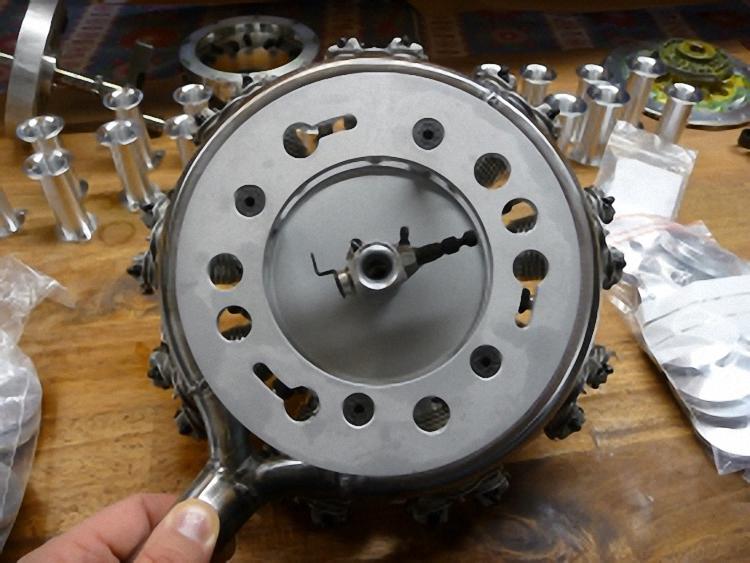
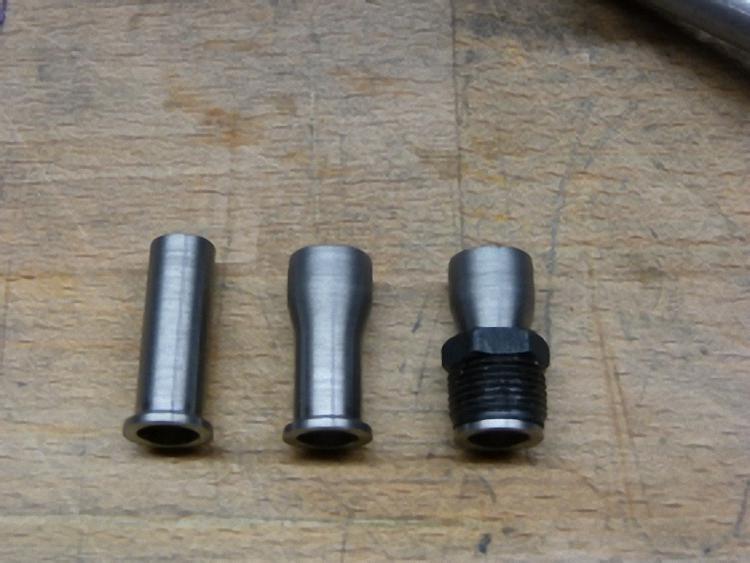
Speziell angefertigte Schweißstutzen und Rohrbögen, gebogen mit unserer Dorn-Rohrbiegemaschine
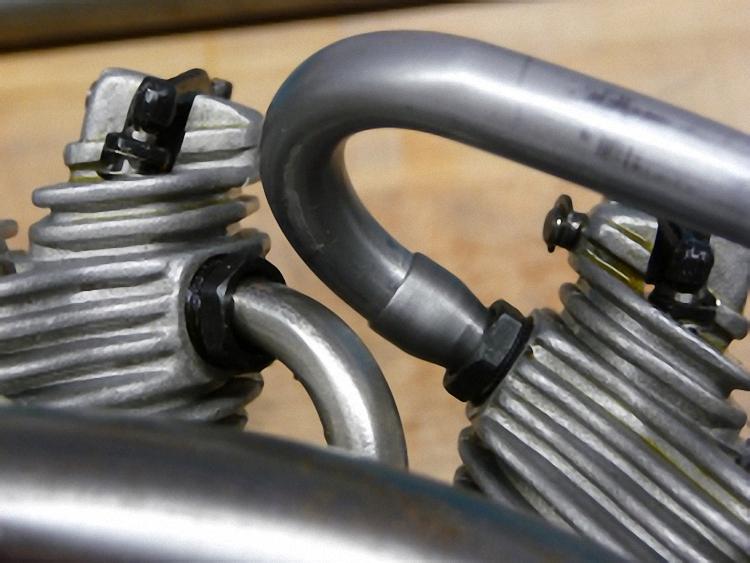
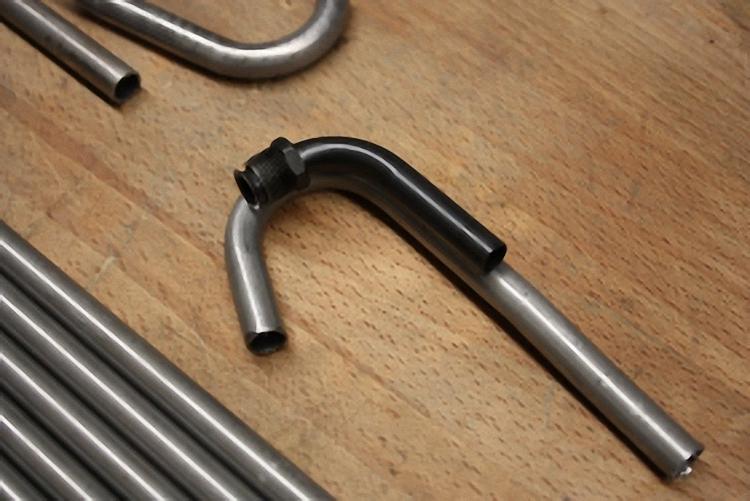
Wir fertigten speziell gebogene Auspuffrohre ... Anpassen, Schweißen, ... Kleine Schellen vervollständigen die perfekte Scaleoptik ...
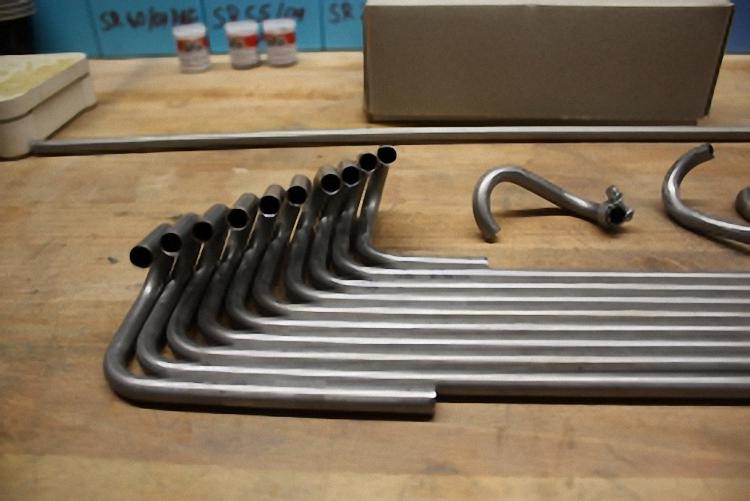
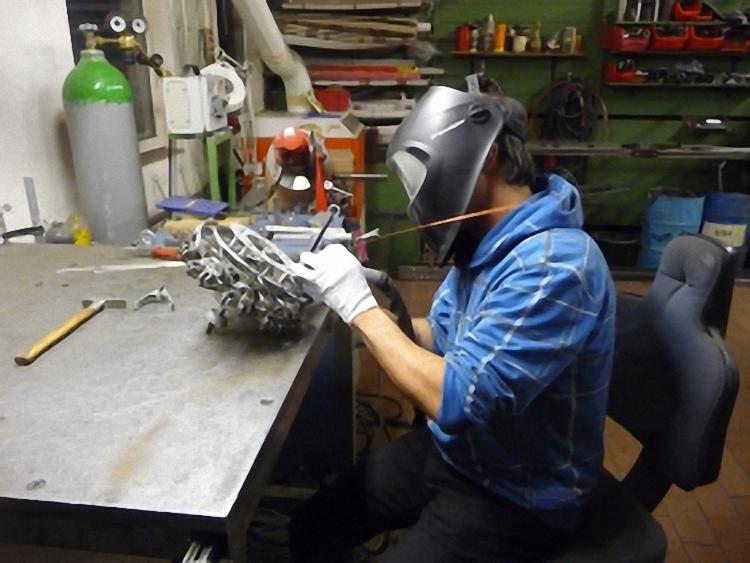
Alle Teile wurden vom Fachmann WIG-geschweißt
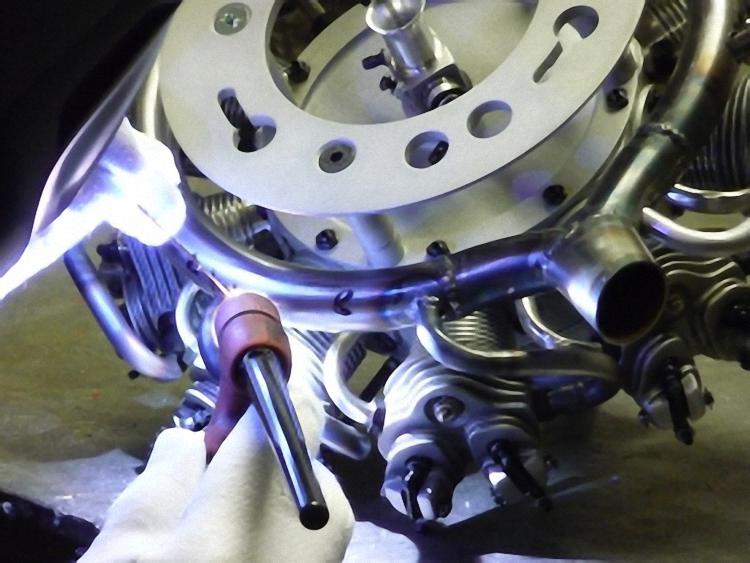
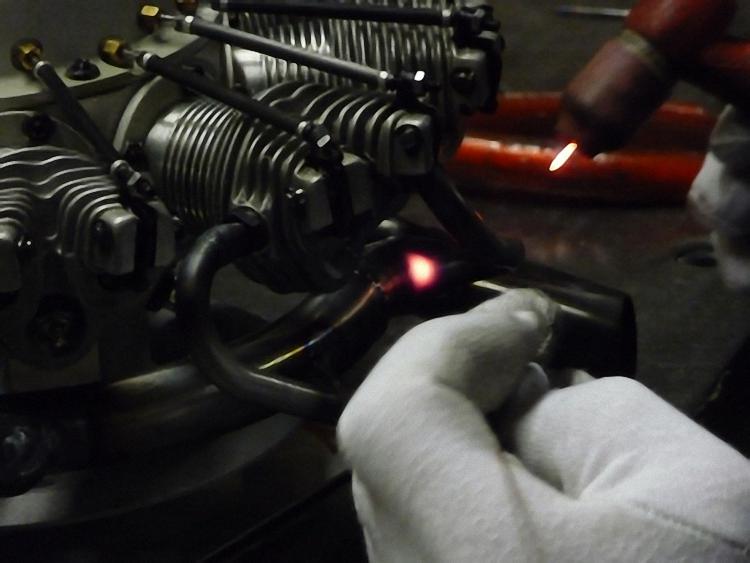
Auf Wunsch haben wir unsere HS Carbonstössel zwecks Massereduzierung und Verschleißminimierung der Nockenscheibe selbst angefertigt.
Das sieht nicht nur gut aus, sondern bringt auch Vorteile.
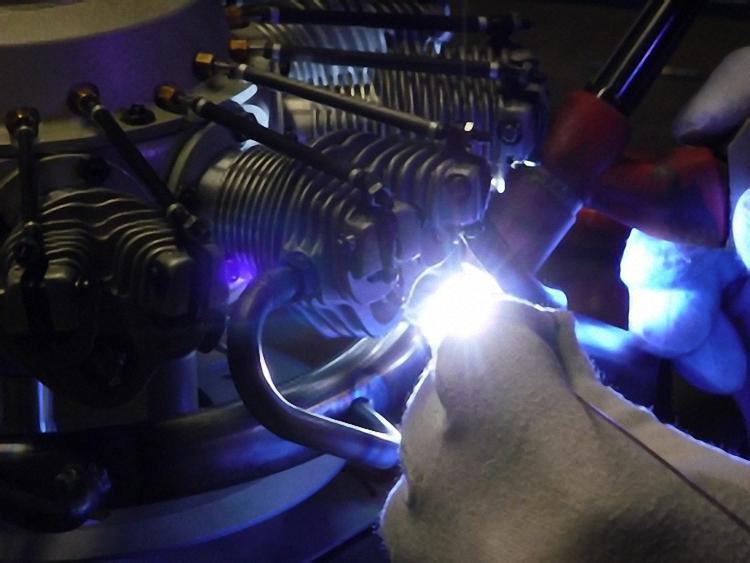
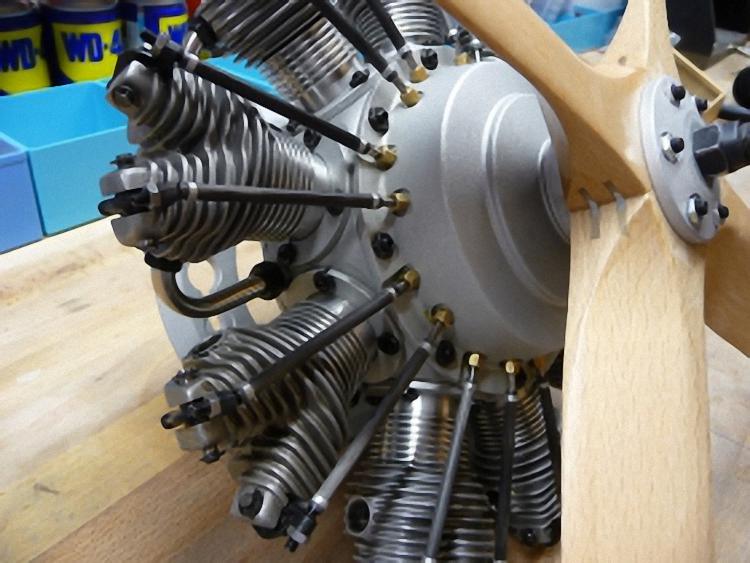
Natürlich wurde auch dieser Sternmotor mit unserem speziellen Motorträger mit Bajonettverschluß ausgestattet.

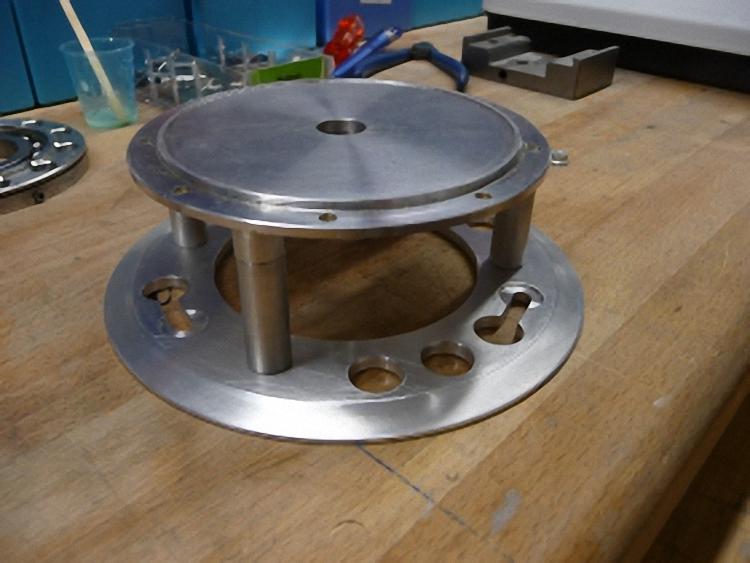
Der Motor erhielt neue Glühkerzenstecker sowie einen Hölzl Glühregler für ein zuverlässiges Laufverhalten.
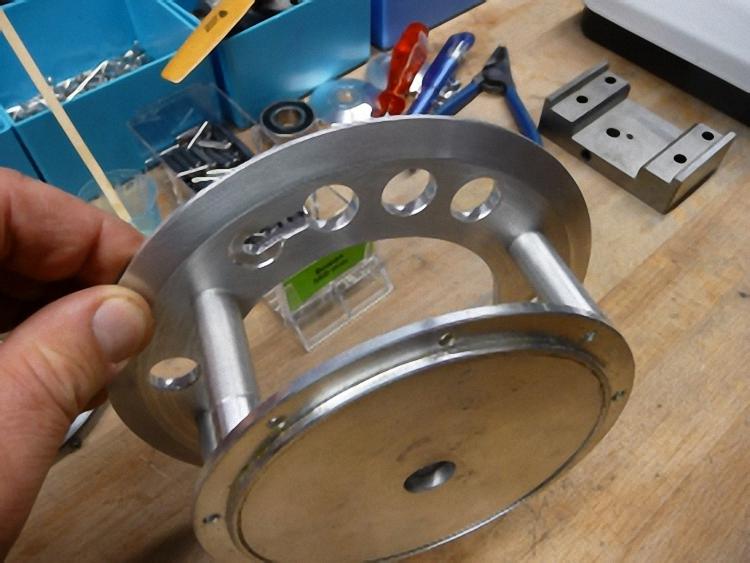
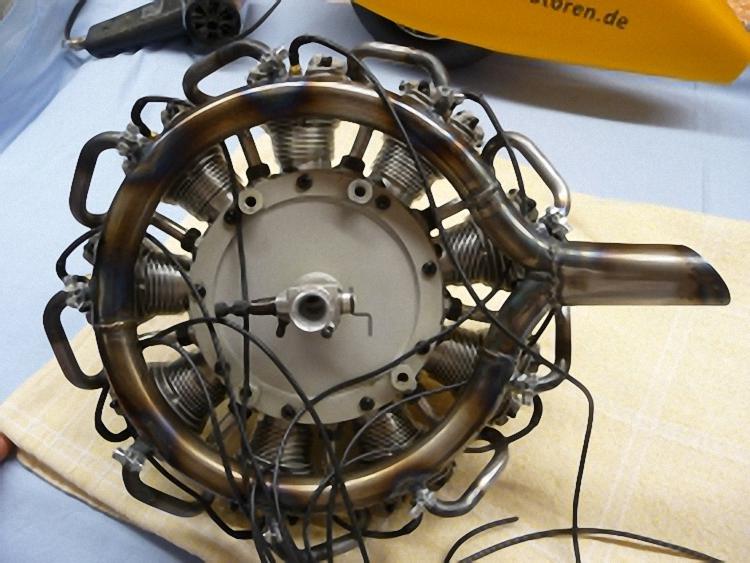
Der sauber verlegte Kabelbaum wird an einer zentralen Stelle zusammengefasst.
Alle Steckverbindungen sind mit Goldkontaktsteckern und dem richtigen Querschnitt versehen.
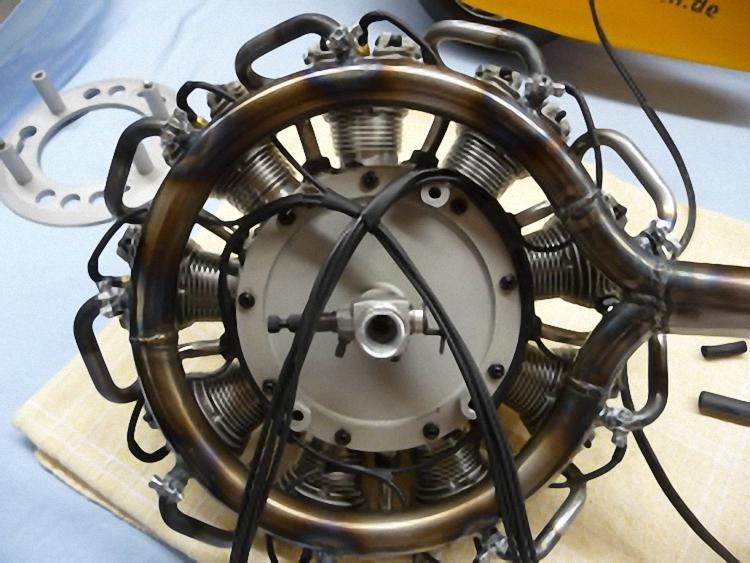
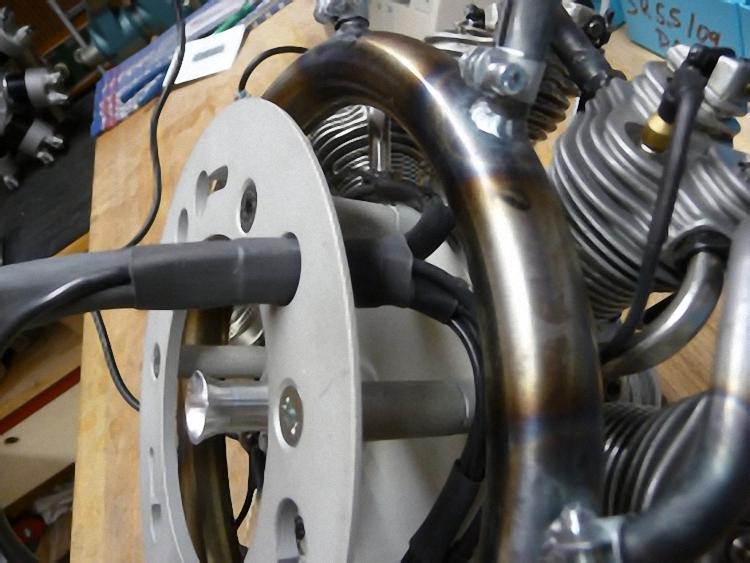
Dieser Motor ist optisch ein echter Hingucker geworden.
Die Ventile lassen sich präzise einstellen und können damit zuverlässig funktionieren.
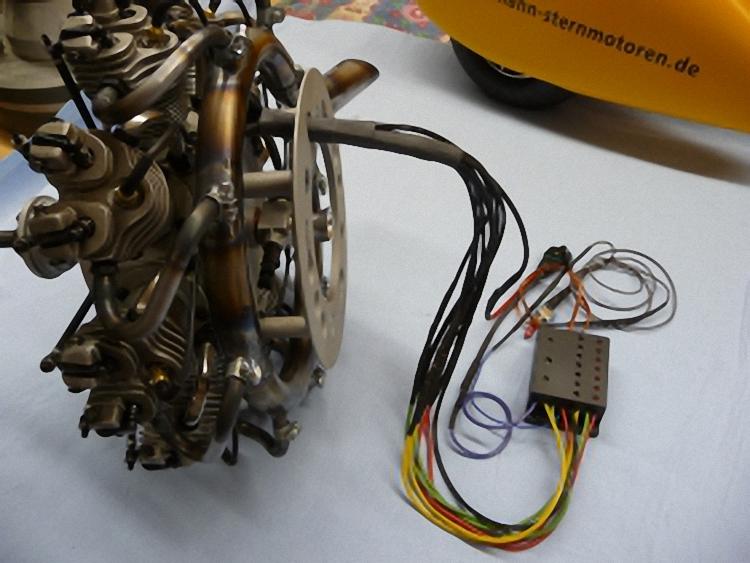
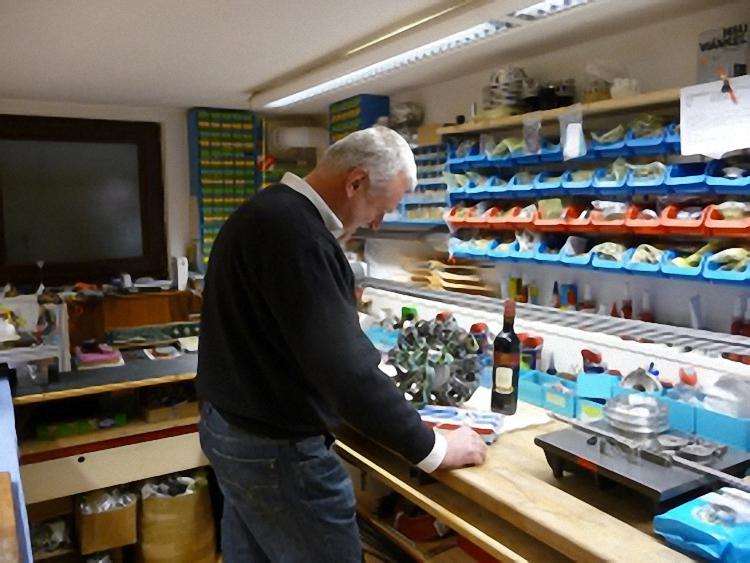
Der Motor wechselt nach ca. einem Jahr Arbeit zurück an seinen stolzen Besitzer Friedrich Wolf
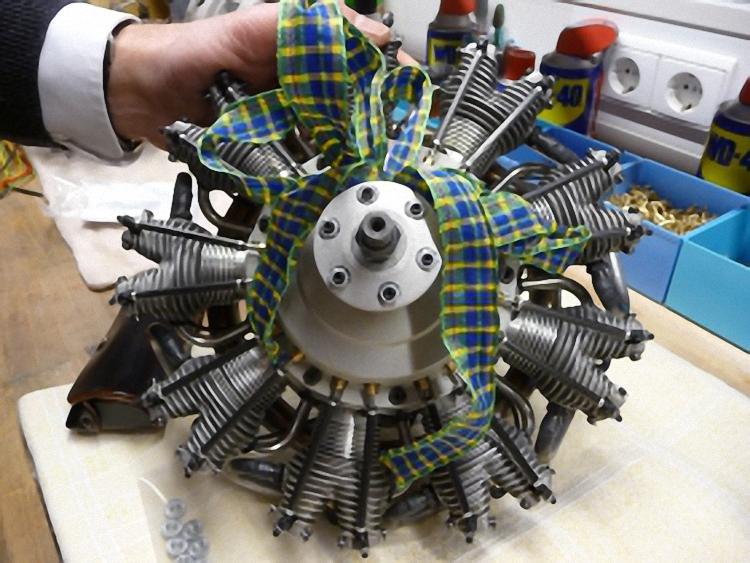
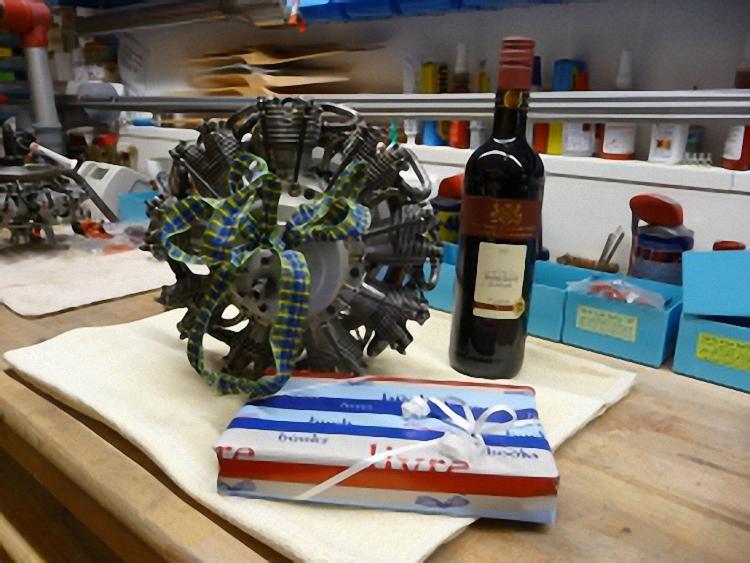
Wir wünschen Friedrich Wolf ein gutes Gelingen des PZL M18 Projekts.
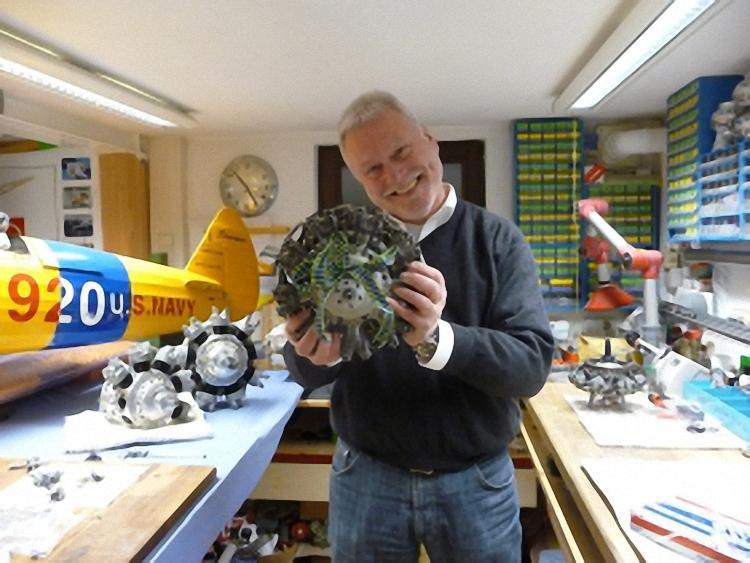
Seidel-UMS ST 7-250B Umbau
Die Vorgeschichte
An unserem zweiten Sternmotorentreffen zeigte Klaus Uhl (Sternmotorenfanatiker) mir seine neueste Errungenschaft, einen Seidel-UMS ST 7-250B, gekauft bei Seidel Triebwerke in Malsch bei Karlsruhe. Ein Motor aus der zweiten Serie mit gefrästen Zylinderköpfen.
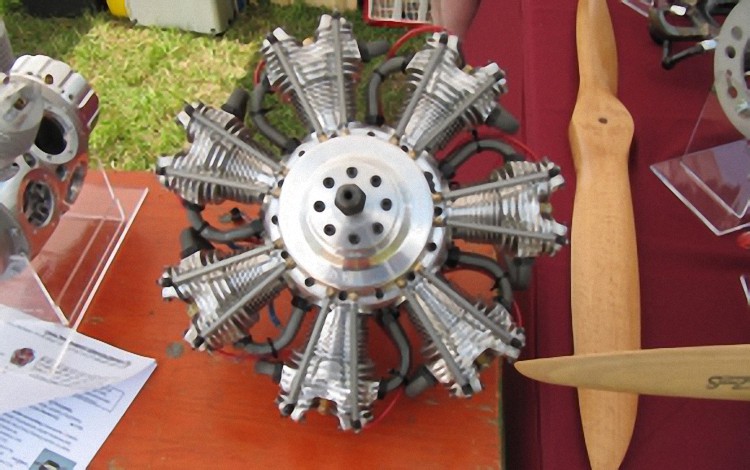
Nach ein paar Monaten rief mich Klaus an und erzählte mir, er habe einen Anruf von Wolfgang Seidel bekommen, dass die Ventile bei dieser Serie der UMS ST 7-250B brechen würden und die Nadellager schadhaft, so wie die Stösselstangen aus zu weichem Alu gefertigt sind und ausgetauscht werden müssen. Er könne die Reparatur nicht übernehmen, obwohl die Garantiezeit moch nicht abgelaufen war. Die Teileversorgung könne er jedoch garantieren.
Klaus bat mich, die Reparatur sowie weitere Umbauten durchzuführen. Dem kam ich gerne nach. Ist er zudem ein treuer Teilnehmer und Helfer bei den Sternmotorentreffen.
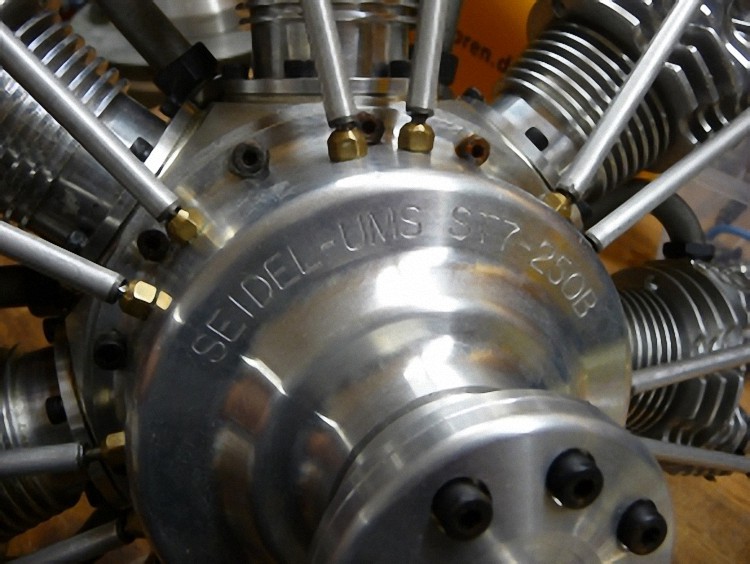
Zuerst habe ich mich an die neue Konstruktion der Motorträgerplatte gemacht. Die Löcher zur Verschraubungen am Motorspant blieben unverändert. Ich entschloss mich eine zweitilige Platte anzufertigen, damit die Zündung einen sicheren Sitz hat.
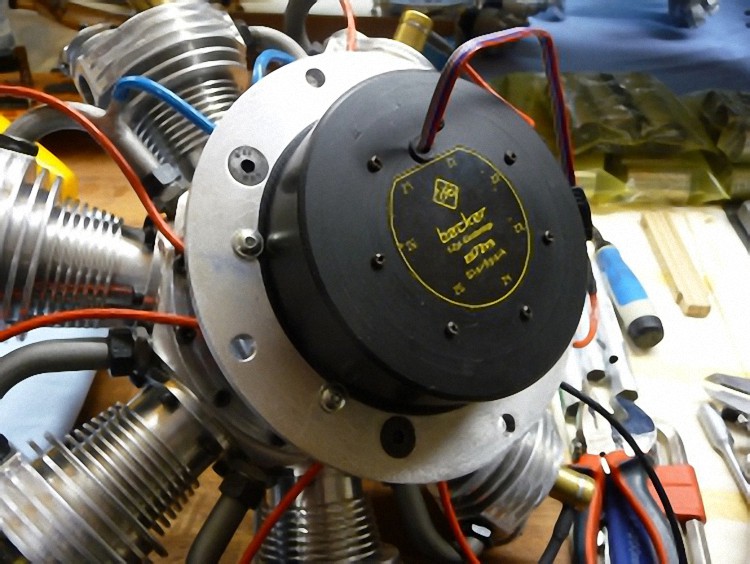

Die Originalbefestigung der Zündung wurde mit nur drei Schrauben fixirt. Nach näherer Kontrolle stellte sich zudem heraus, das die Originalplatte komplett krumm und verbogen war.
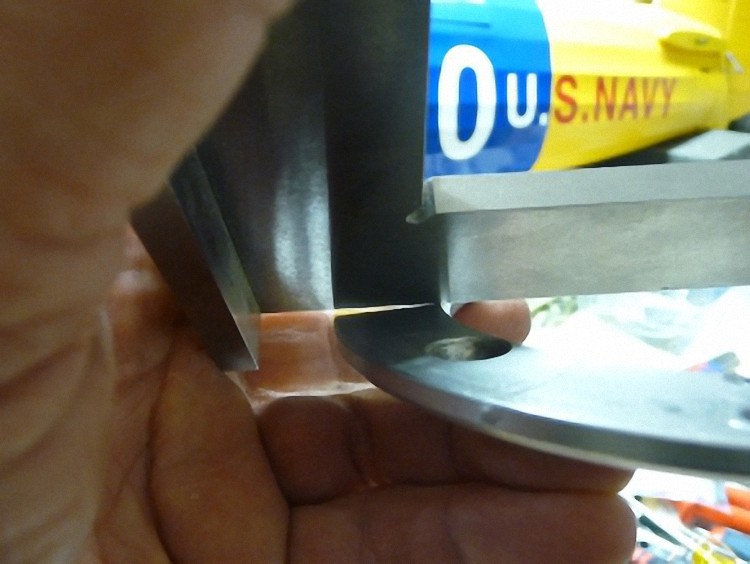
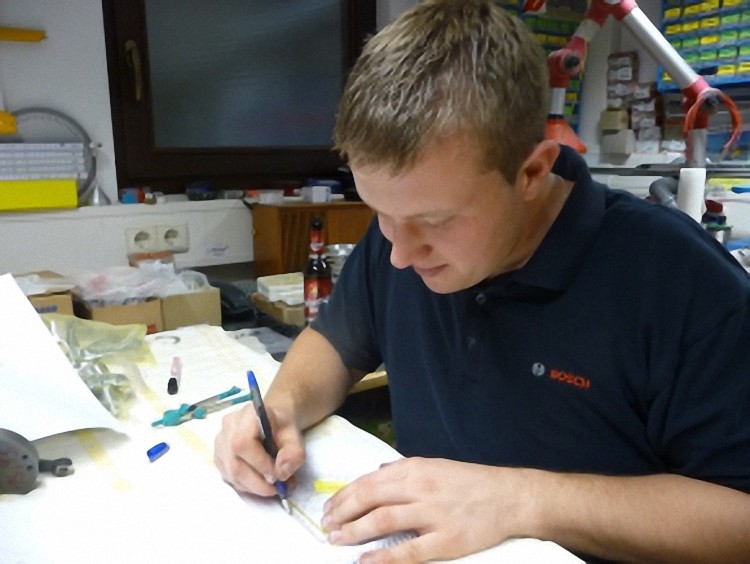
Platte wird vermessen...
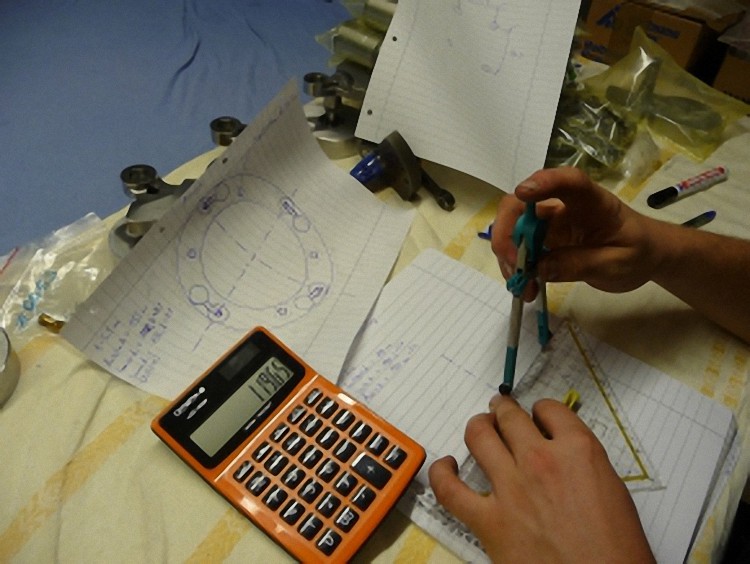
... und gezeichnet
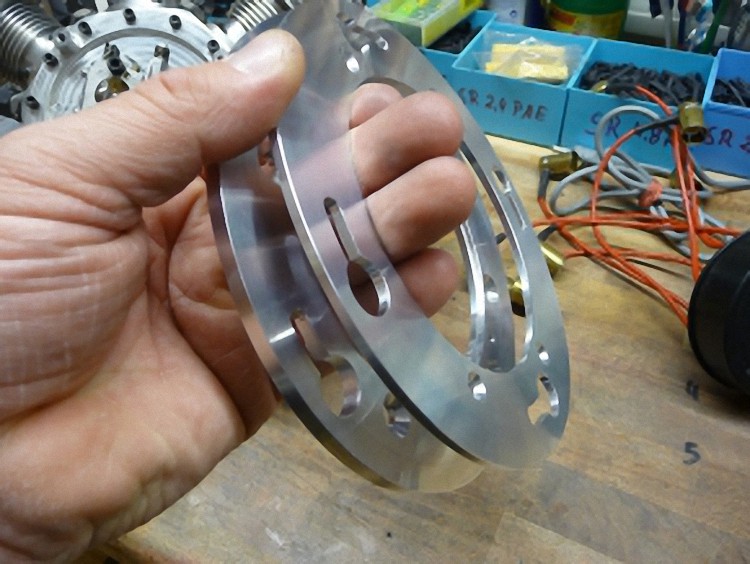
neu angefertigte Motorträgerplatte...
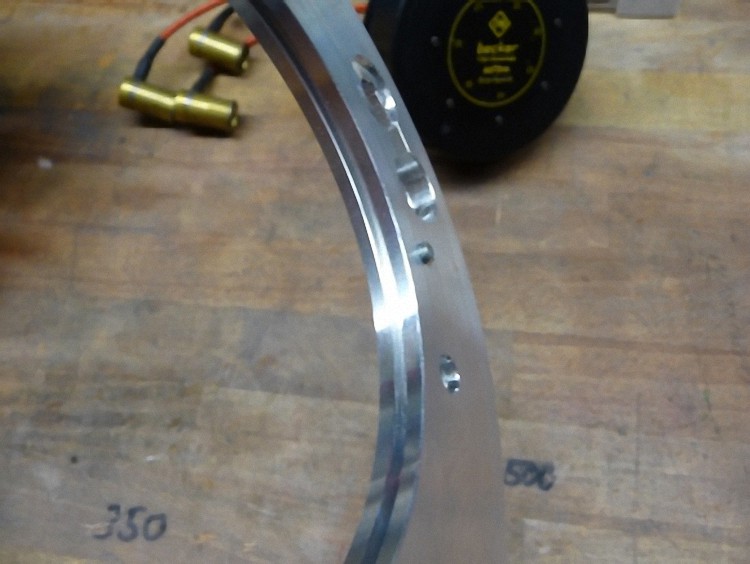
In der Ringnut sitzt die Zündung
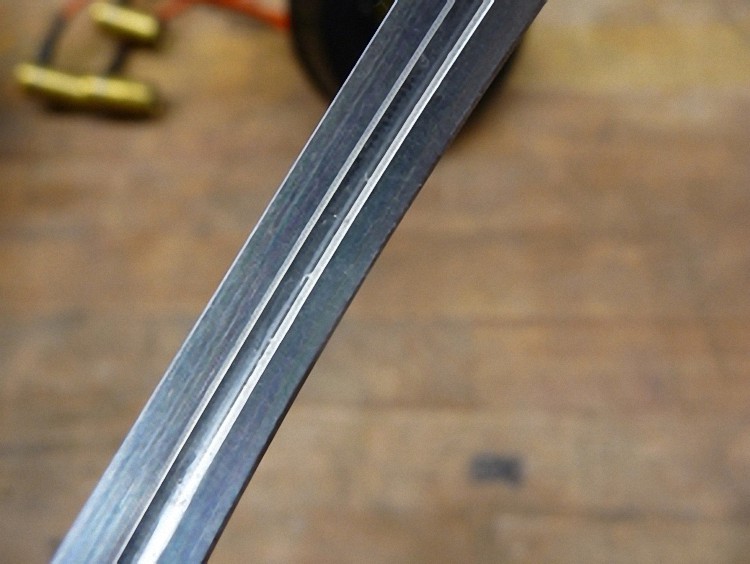
Ringnut für Zündanlage
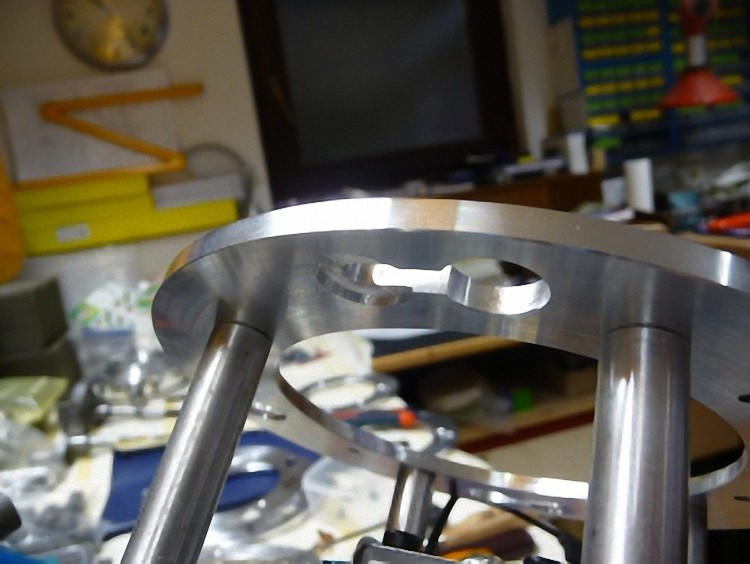
Bajonettverschluss
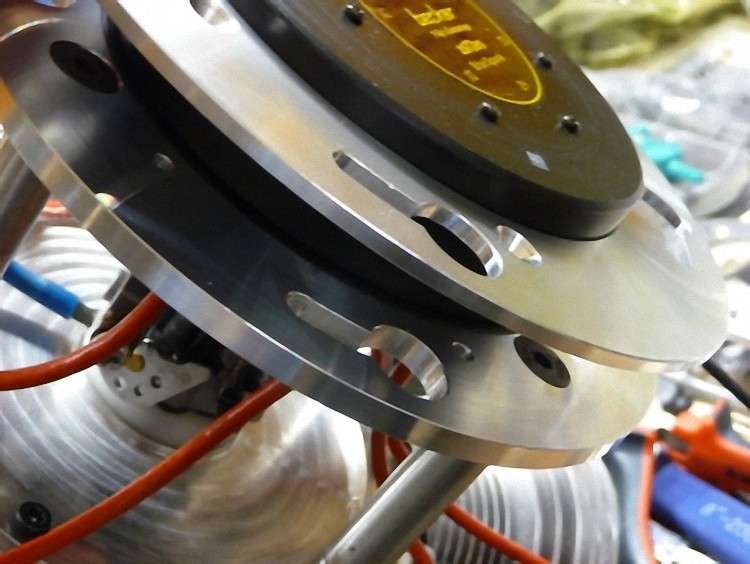
Nun erfolgte der testweise Einbau der Zündanlage sowie der Härtetest für den Bajonettverschluß. Dieser funktionierte auf Anhieb und passte genau in den ausgefrästen Teil.
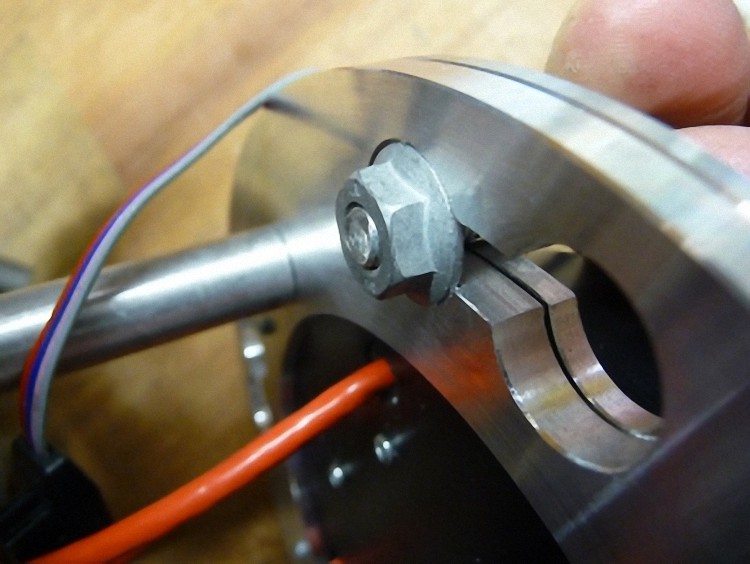
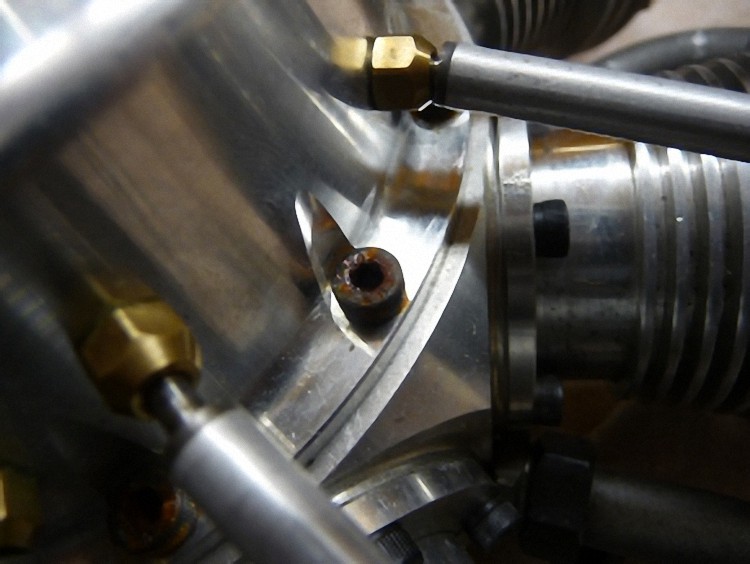
Die verrosteten Schrauben des Nockengehäuses waren mir von Anfang an ein Dorn im Auge. Leider hatten sich die rostigen Stellen tief ins Aluminium eingefressen und mussten regelrecht rauspoliert werden.
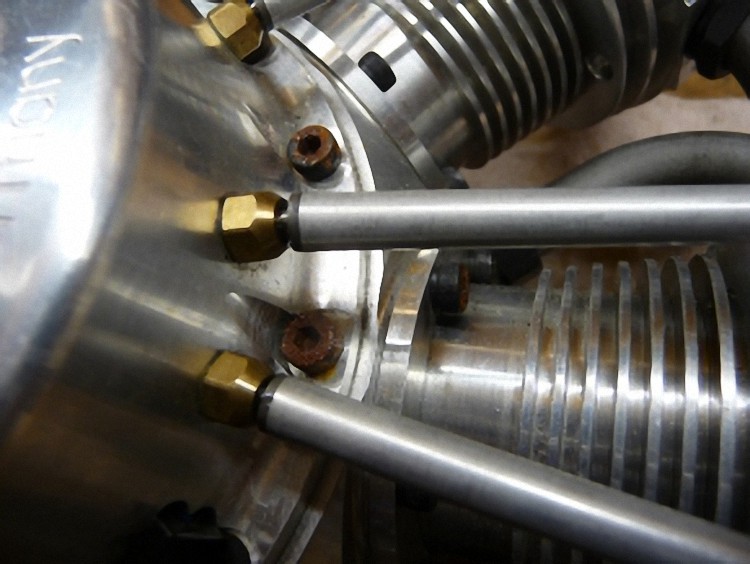
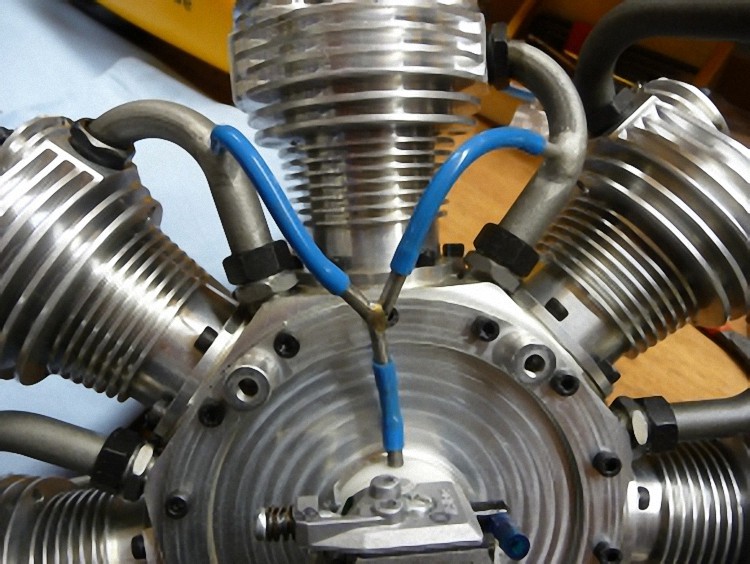
Bei weiterer Überprüfung stellte ich fest, dass der Schlauch zum Vergaser die den Impuls für die Membrane geben, angerissen war. So konnte der Motor, wenn überhaupt, nur schwer laufen.


Vor dem Zerlegen des Motors hatte ich noch die Zündung vermessen, wie der Sensor zum oberen Todpunkt/Zündungstakt ausgerichtet ist. Dazu hatte ich mit von Firma Becker ein elektronisches Helferlein anfertigen lassen.
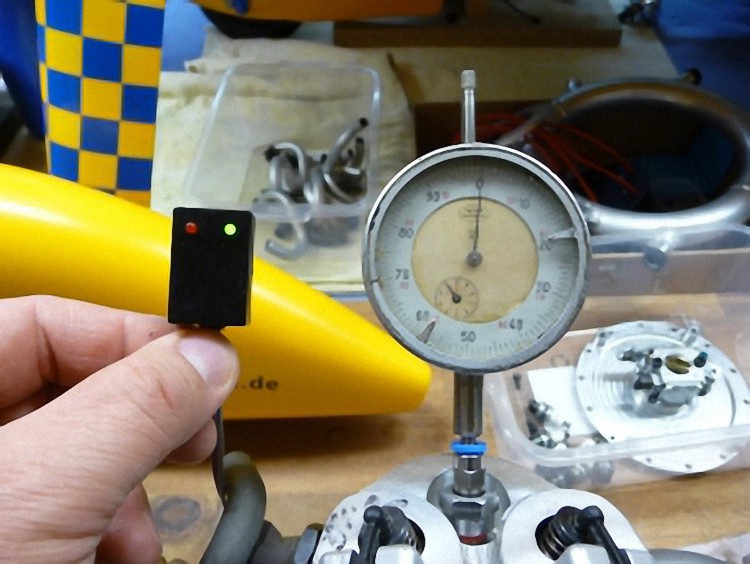
Die Zündung war also 15° vor OT eingestellt. Normalerweise sollten es 0° auf OT sein, damit der Motor beim anwerfen nicht zurück schlägt. Die Zündung stellt dann alle 1000 U/min. auf ca. 3,9° Frühzündung (d.h. bei 5.000 U/min = ca. 19,5°).
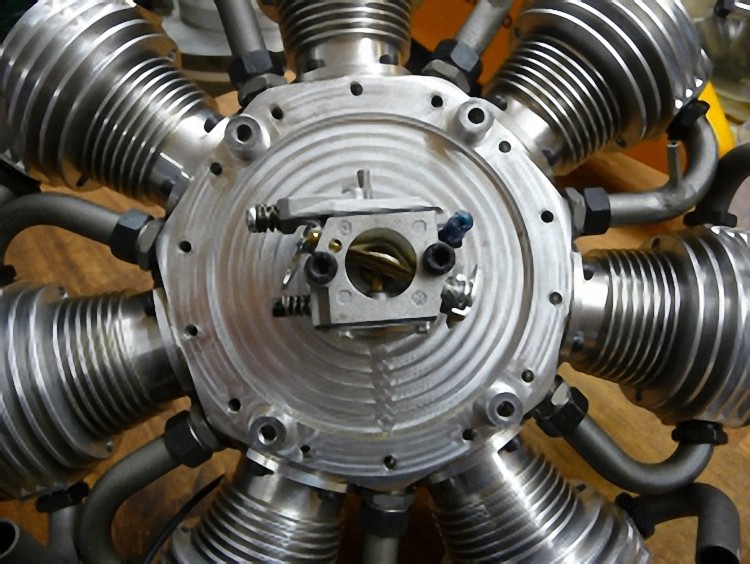
Demontage Heckplatte mit Vergaser und Aufnahme Motorträger

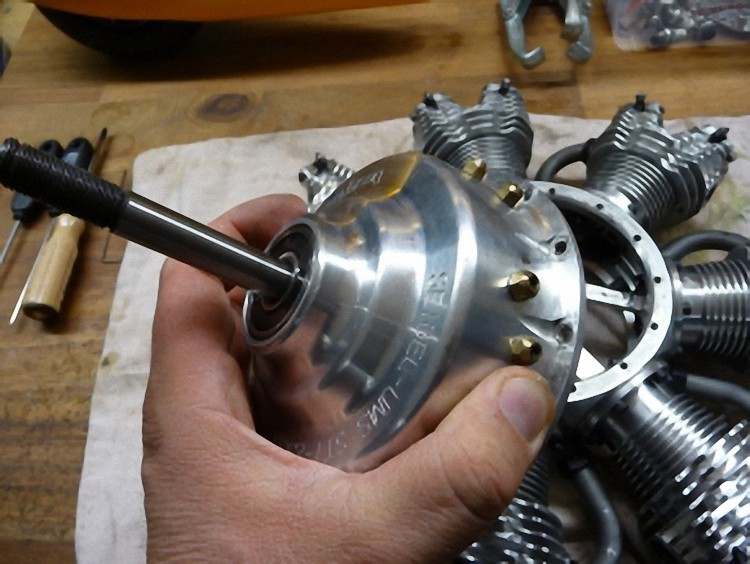
An der Vorderseite wurde nun das Nockengehäuse abgeschraubt.
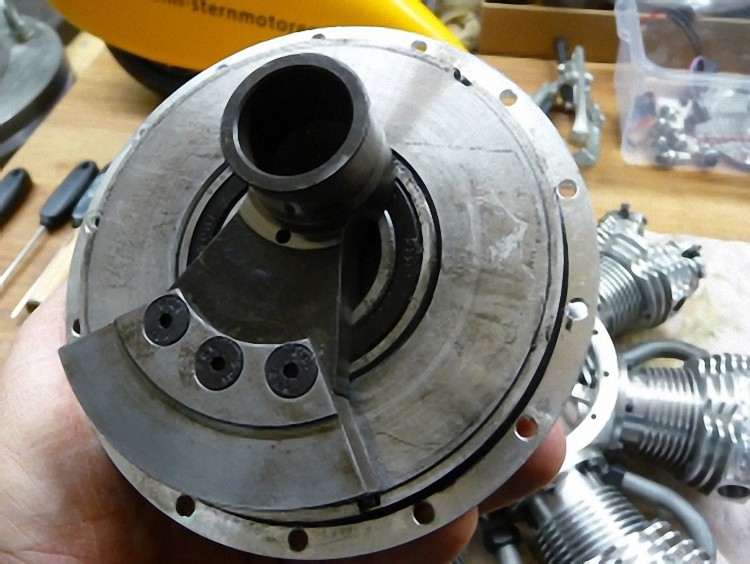
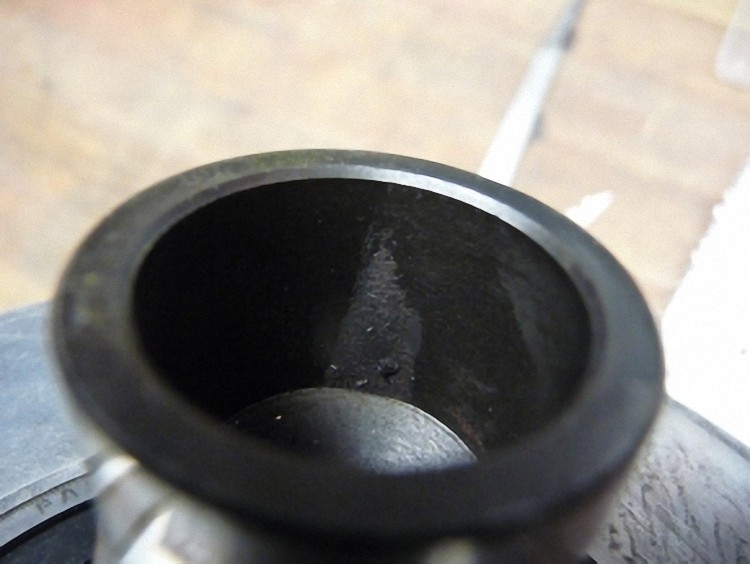
Beim Blick in den Hubzapfen musste ich feststellen, dass noch Metallspäne der Herstellung vorhanden waren. Diese habe ich sauber entfernt.
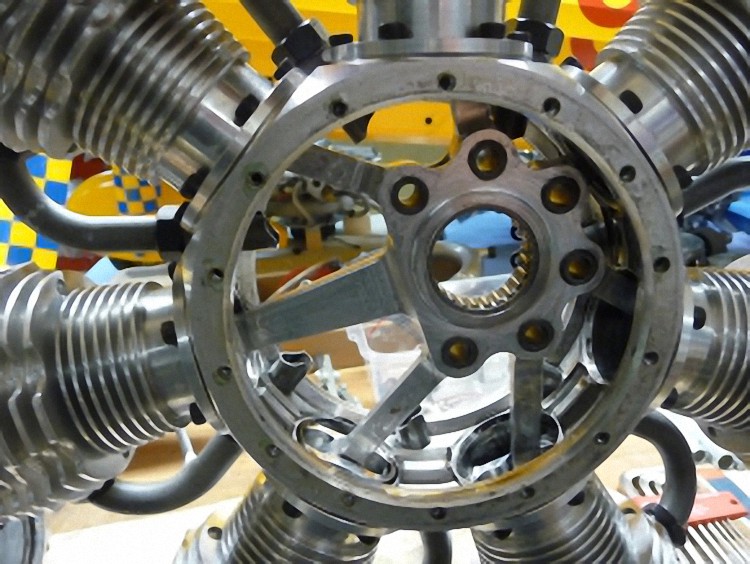
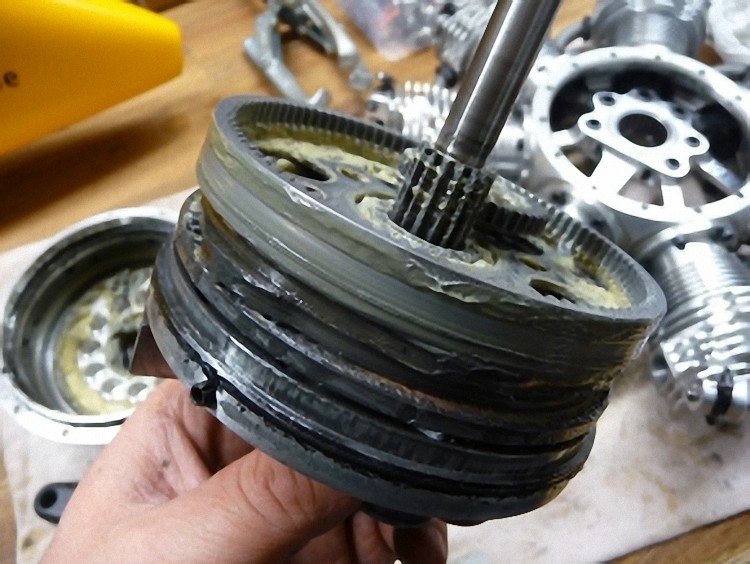
Ausgepresste Kurbelwelle mit Nockenkranz, -scheibe und Zündmagneten. Es ist erstaunlich wie wenig Fett im Gehäuse war. Obwohl der Motor neu und nur im Werk gelaufen ist. Glücklicherweise hat es das Fett nicht bis in die Erleichterungsbohrungen des Deckels geschafft.
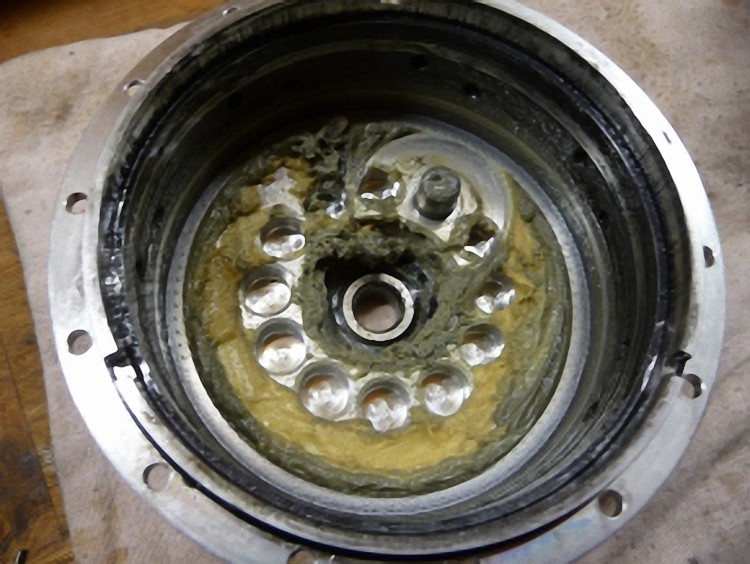

Hier gut zu sehen: Die Aluminiumscheibe welche die Magnete aufnimmt. 21+3 negativ gepolte zur Erkennung des ersten Zylinders. Da die Nocke drei Nockenpaare hat und 1:6 untersetzt ist.
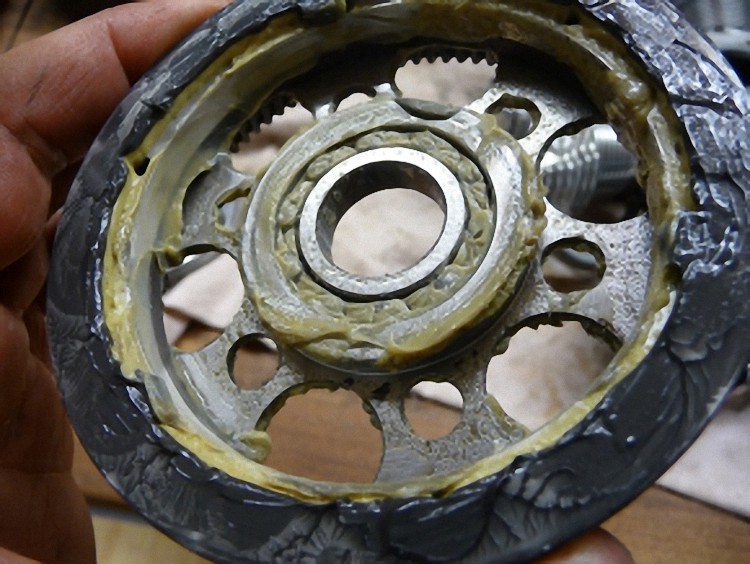
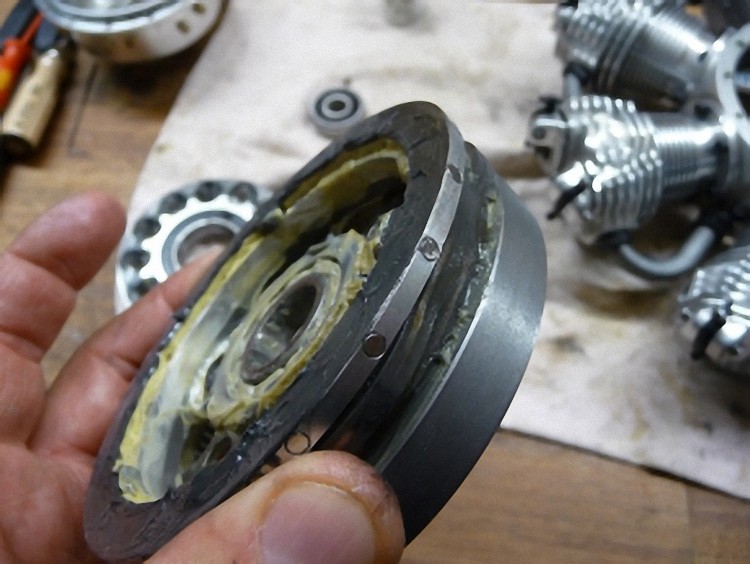
Der Nockenkranz macht einen guten Eindruck. Alle Zähne sind glücklicherweise vorhanden :-)
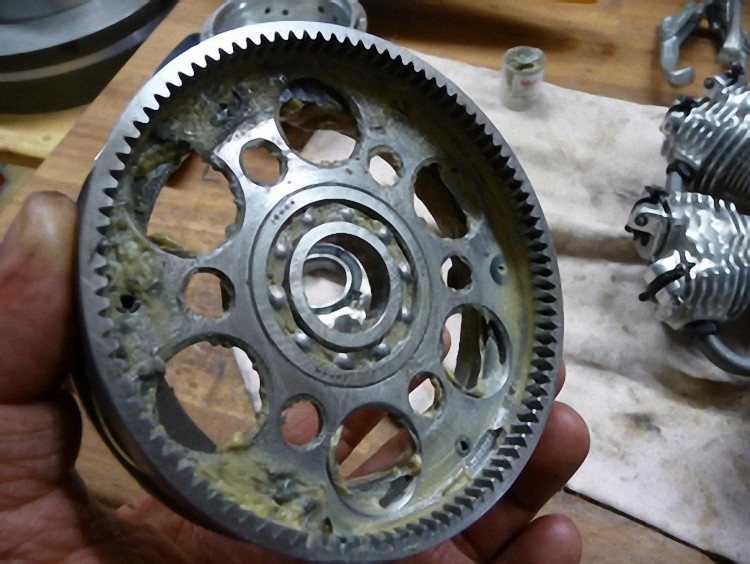
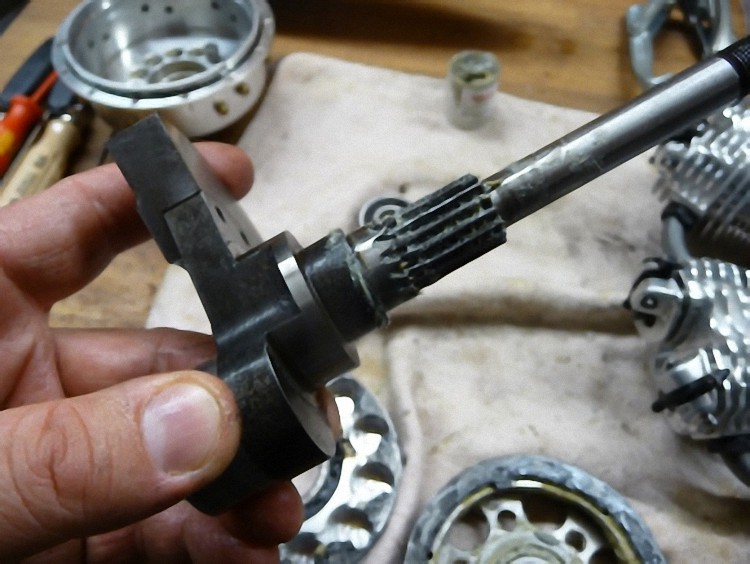
Die Kurbelwellenverzahnung sieht ebenfalls gut aus. Die Kurbelwellenwange ist mit der Kurbelwelle verschraubt. Verwunderlich ist nur, dass die Inder die Gewindetiefe nicht voll ausnutzen.
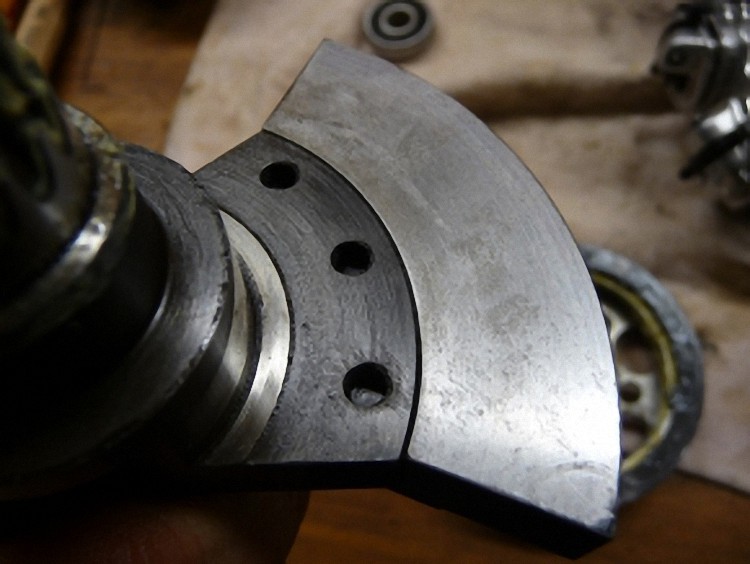
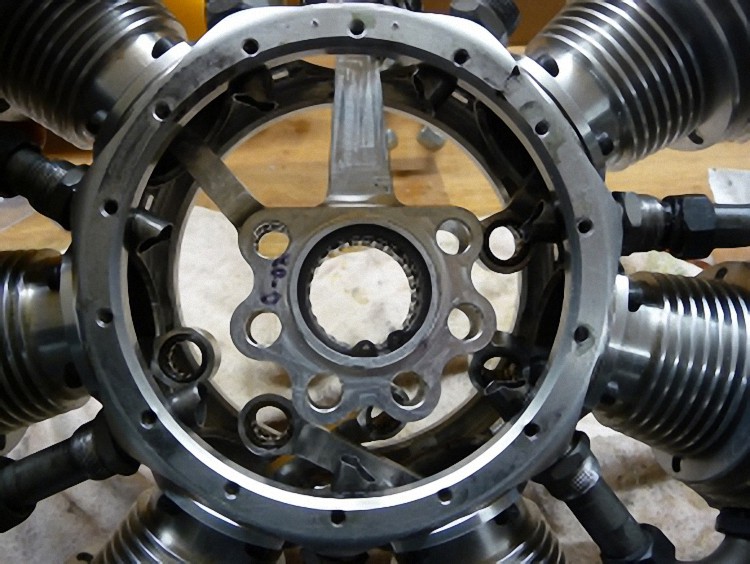
Alle Pleuelbolzen sind gezogen und die einzelnen Zylinder werden demontiert. Schade, dass nur ein Kolbenring verbaut ist. Für eine gute und dauerhafte Kompression sind eigentlich zwei Dichtringe notwendig.
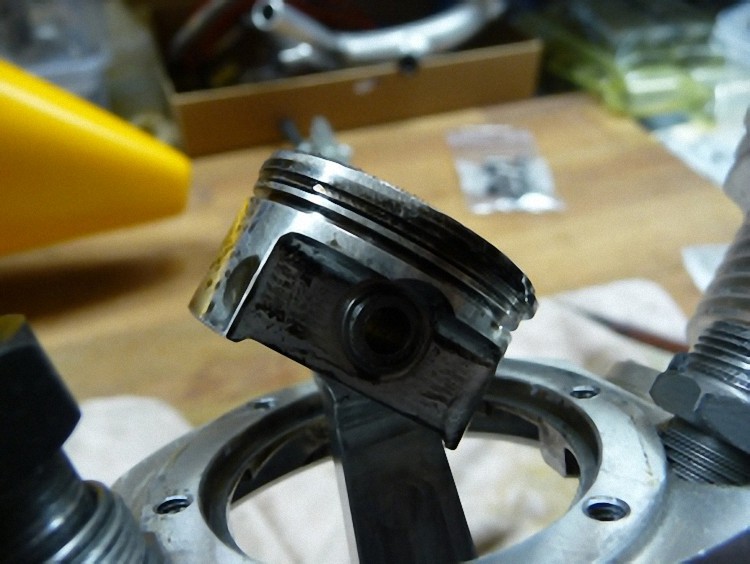
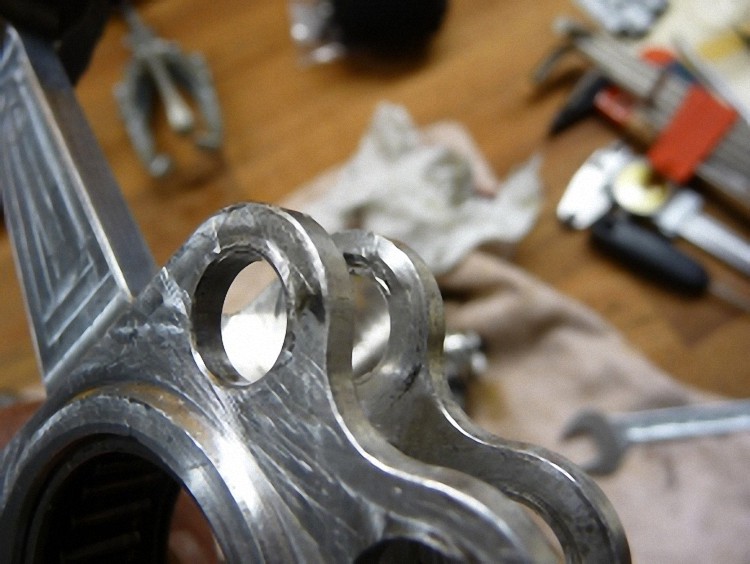
Bei der Montage im Werk wurde der Pleuelbolzen schräg eingepresst. Hier musste ich nacharbeiten.
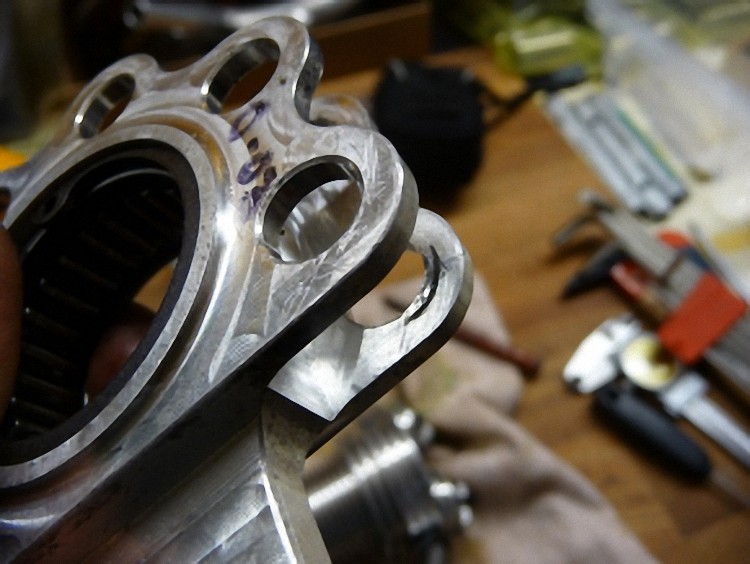
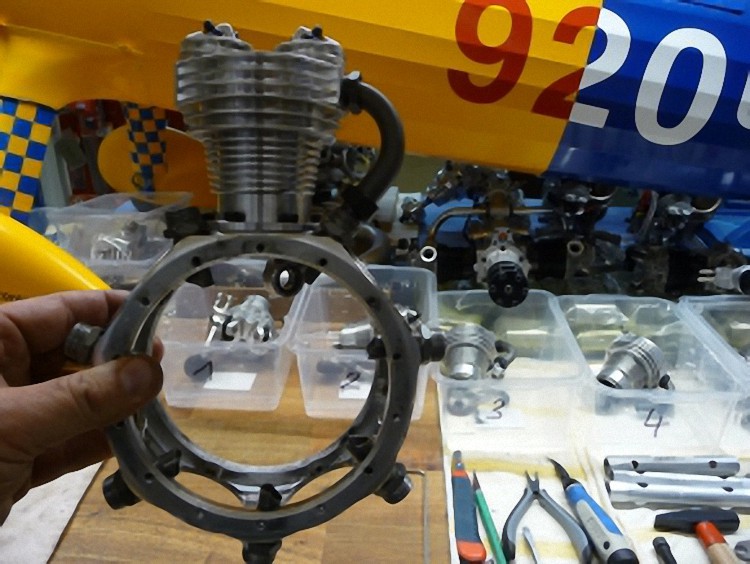
Alle Teile sind zerlegt und sauber verstaut. Es ist sehr wichtig, darauf zu achten, dass alle Teile gepaart bleiben.

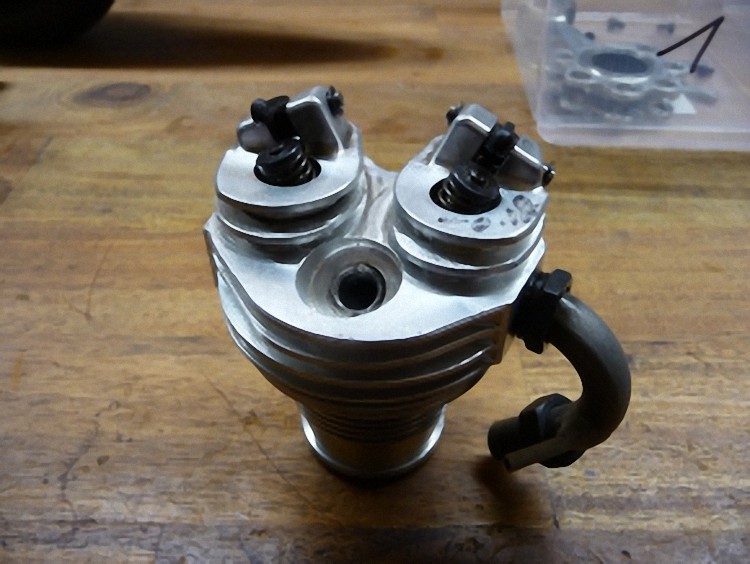
Die Ventile werden nun aus dem Zylinderkopf ausgebaut.
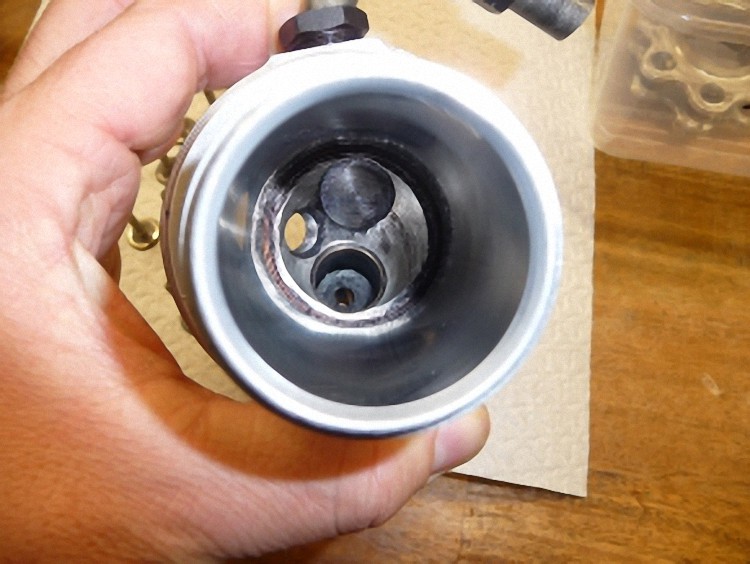
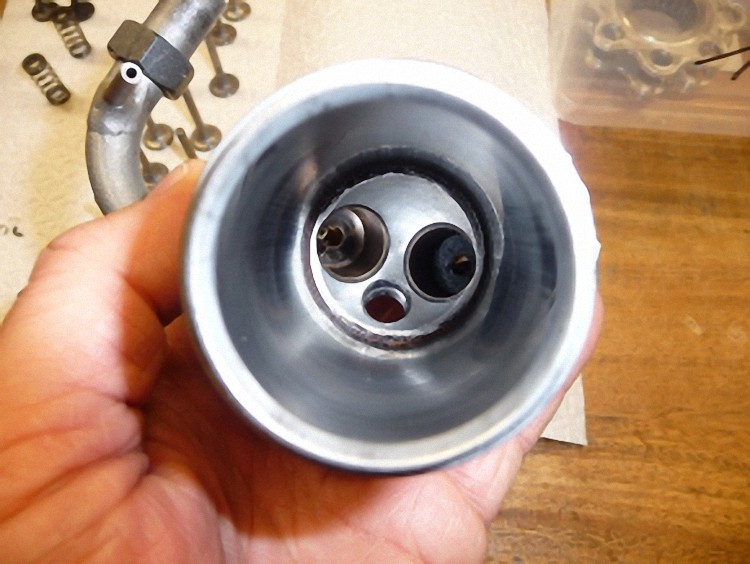
Es ist gar nicht so einfach die kleinen Keile ohne Verluste auszubauen. Einmal nicht aufgepasst und die Keile fliegen durch die Werkstatt.
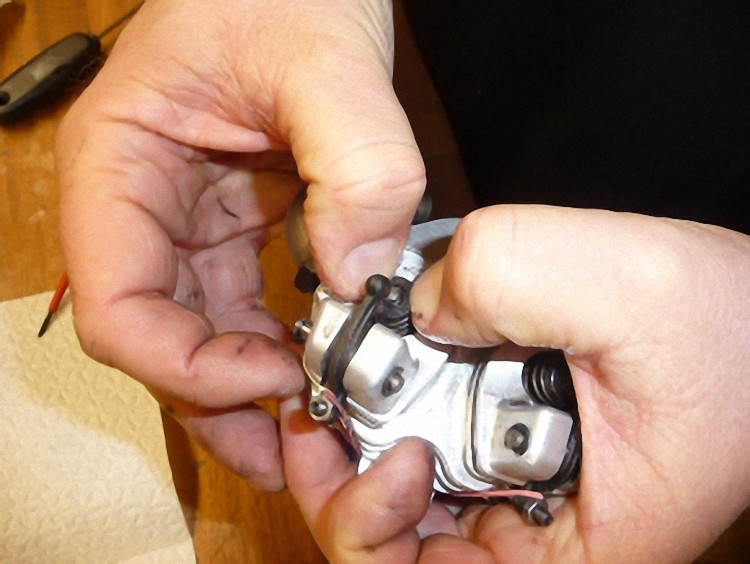

Alle Teile wurden gereinigt und sind nun fertig zum Zusammenbau.
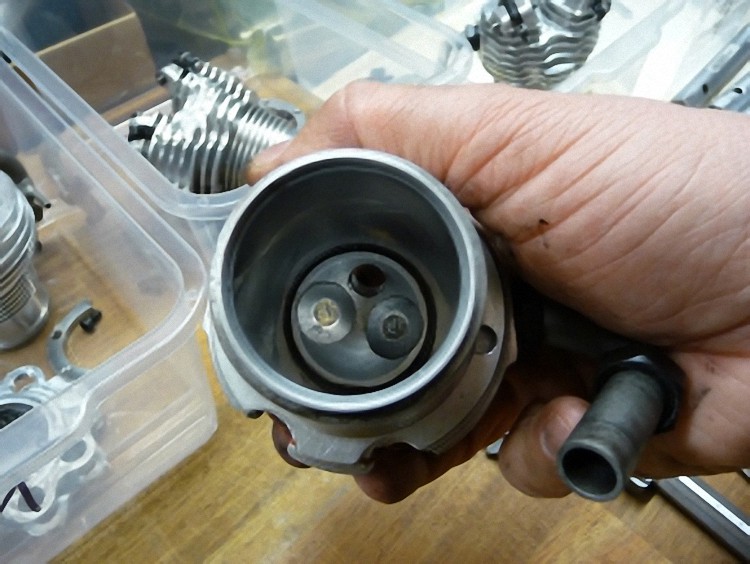

Nun geht es an die Dichtigkeitsprüfung der Zylinderköpfe. Da die alten Teile (Ventile) in den Müll wandern, machen wir einen Bruchtest.
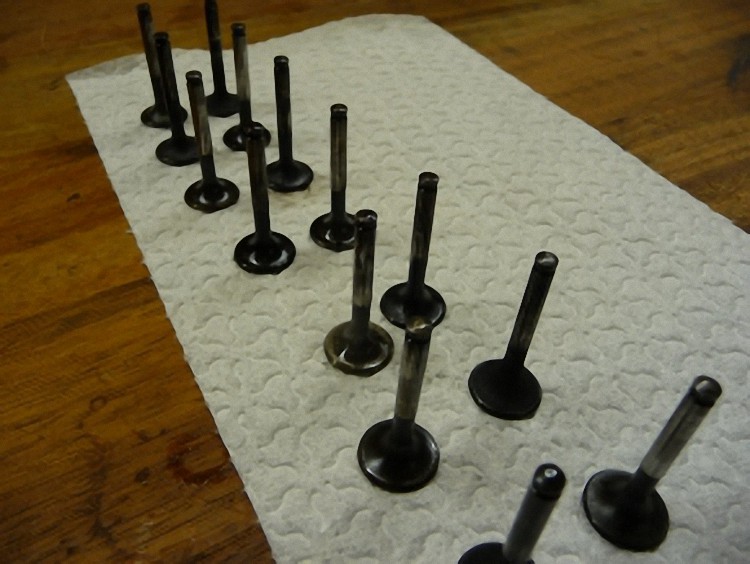
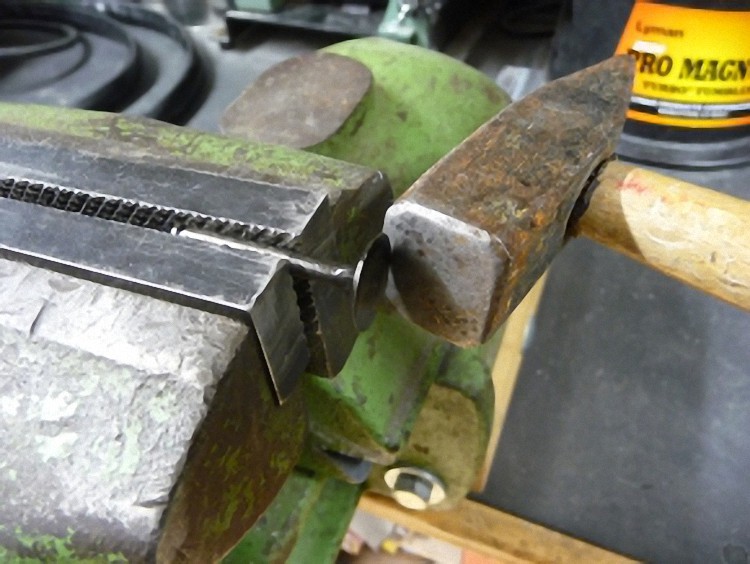
Ein erschreckendes Ergebnis. Die alten Ventile brechen wie Glas und dabei hatte ich nur ganz leicht mit dem Hammer dagegen geklopft.
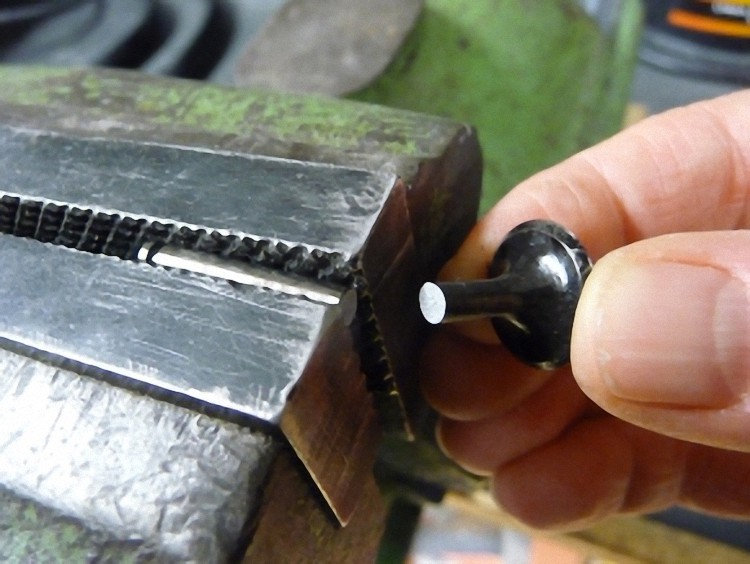
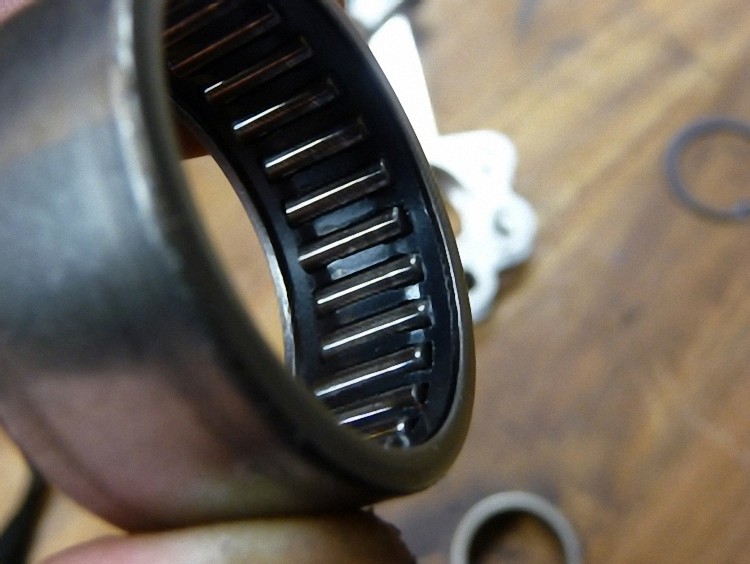
Das indische Nadellager des Mutterpleuels habe ich gegen deutsche INA Nadellager mit breiten Nadeln getauscht. Dies ist bei dieser Baugröße für das Kippmoment auf dem Hupzapfen unbedingt notwendig.
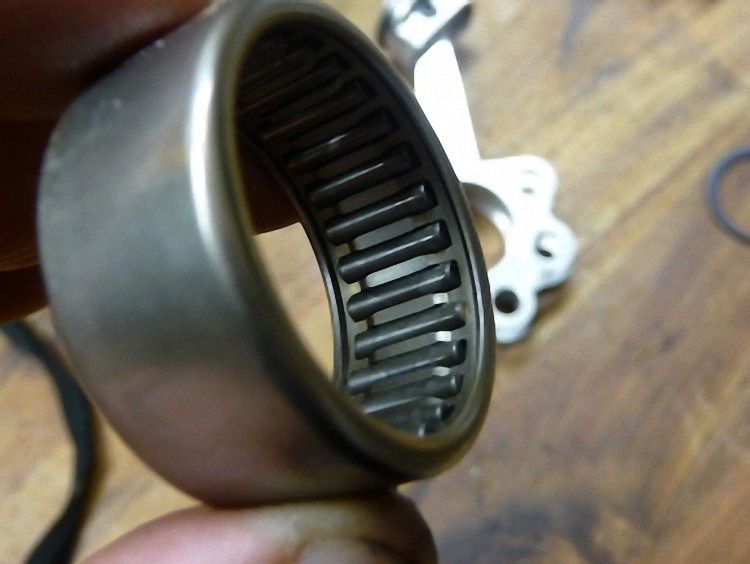
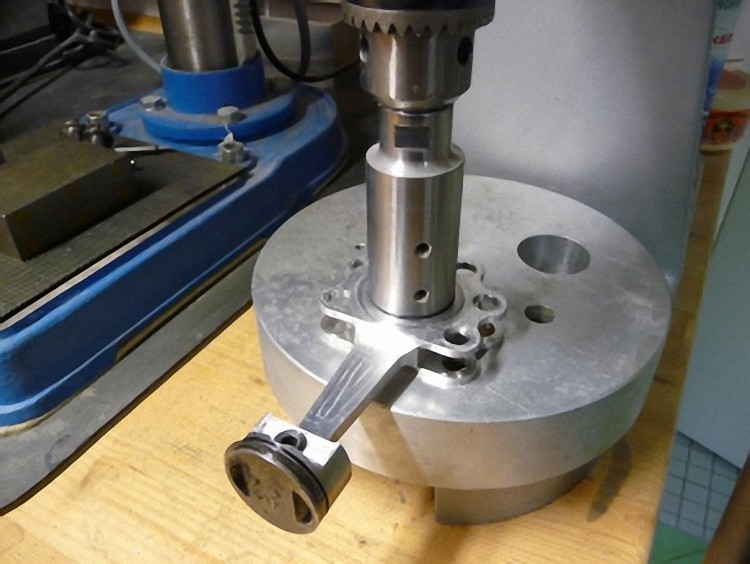
Das neue Nadellager wird nun eingepresst. Das Ergebnis sieht sehr gut aus. Als nächstes prüfen wir ob sich das Lagerspiel des neuen Lagers auf dem Hubzapfen der Kurbelwelle verändert hat.
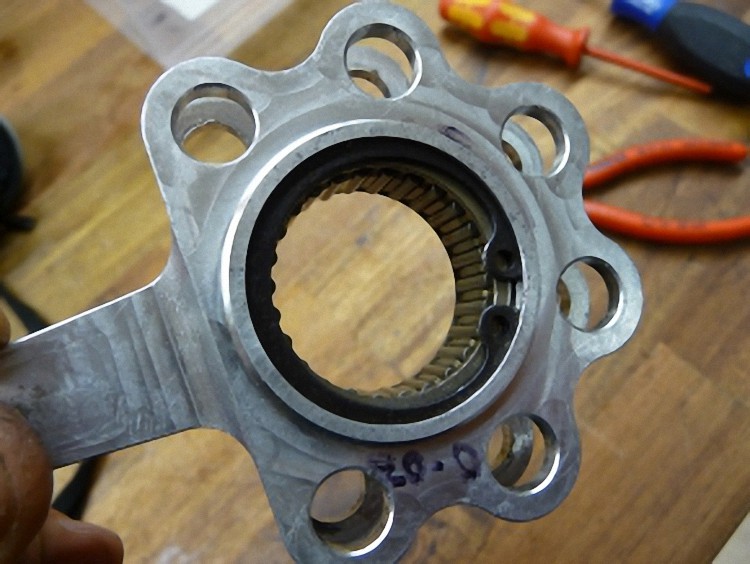

Alles passt. Die Toleranzen sind unverändert. Das kleine Nadellager im Pleuelkopf habe ich ebenfalls ausgetauscht. Laut Aussage von Wolfgang Seidel brechen hier die Nadelkäfige auf und die Nadeln machen sich im Motor selbständig --> Totalschaden :-(
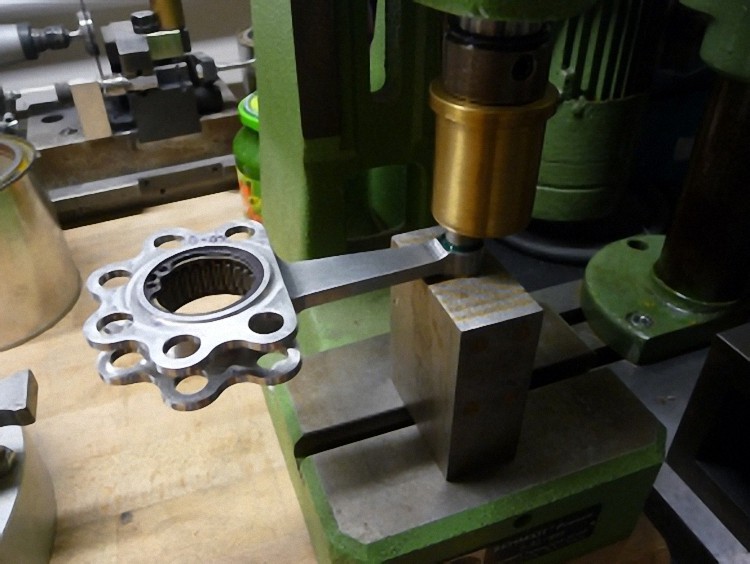
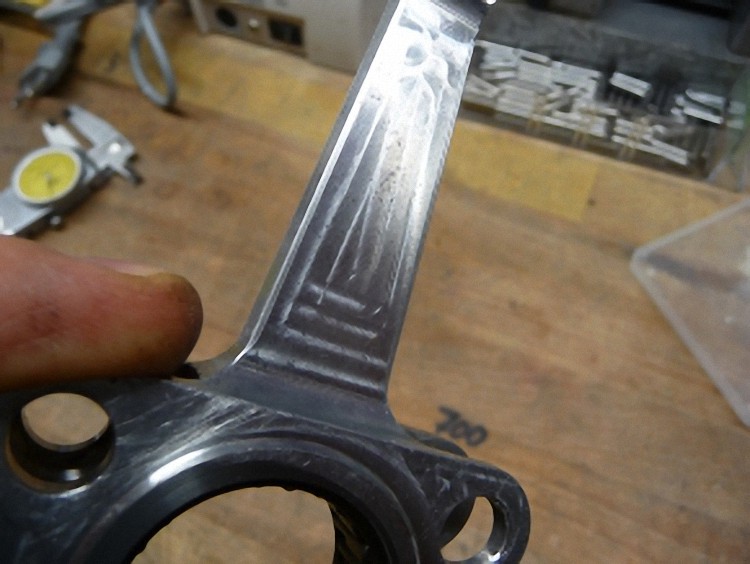
Was mir persönlich überhaupt nicht gefällt, sind die Frässpuren auf dem Mutterpleuel. Dies ist ein hoch beanspruchtes Bauteil, das keine Kerbwirkung durch maschinelle Bearbeitung haben darf. Also komplett nacharbeiten und polieren.
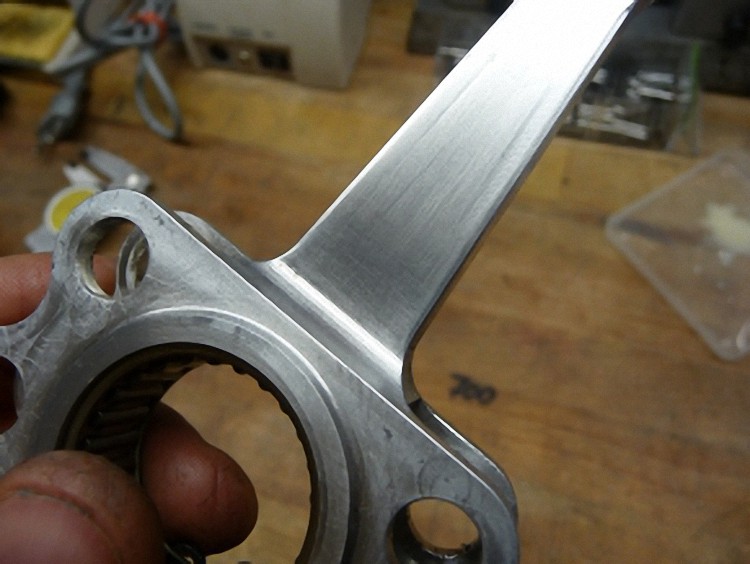
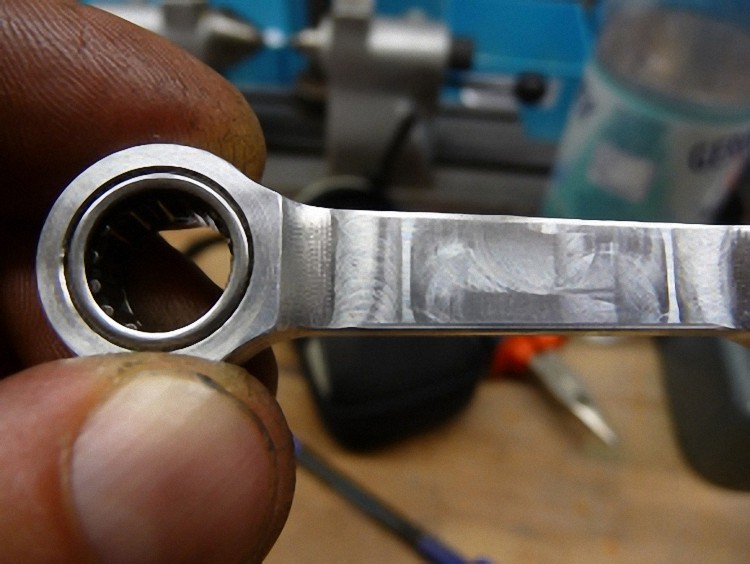
Bei den Nebenpleuel habe ich mir diese Mühe erst gar nicht gemacht und die Nadellager ausgepresst. Ich habe sie komplett entsorgt und durch neue Nebenpleuel ersetzt.
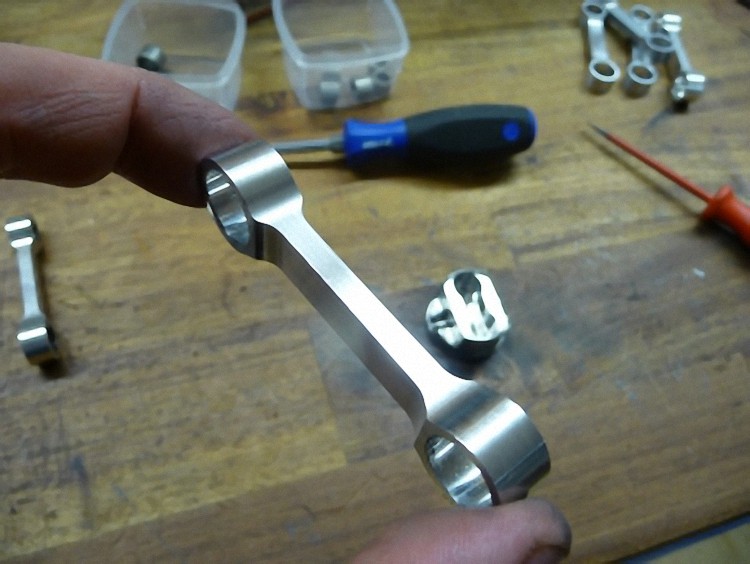
Der Übergang von der Pleuelstange zum Pleuelauge war total zernagt (wie mechanisch mit der Feile nachgearbeitet) und das Aluminium an sich butterweich. Das heißt nicht, dass es nicht funktioniert, jedoch entspricht es nicht meinem technischen Verständnis, diese wieder einzubauen.

So sieht ein neues und frisch poliertes Pleuel aus. In dieses habe ich ebenfalls deutsche INA-Nadellager verklebt und eingepresst.

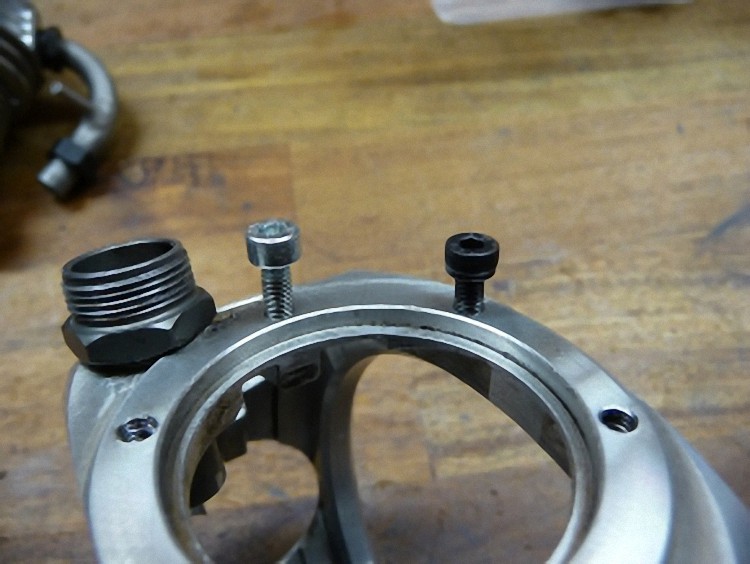
Bei den Zylinderfußschrauben im Motorgehäuse waren die Gewinde nicht tief genug geschnitten. Die Bohrungen habe ich also tiefer gesetzt und das Gewinde nachgeschnitten. Der Zylinder wurde mit Flächendichtmittel zum Motorgehäuse hin neu abgedichtet.
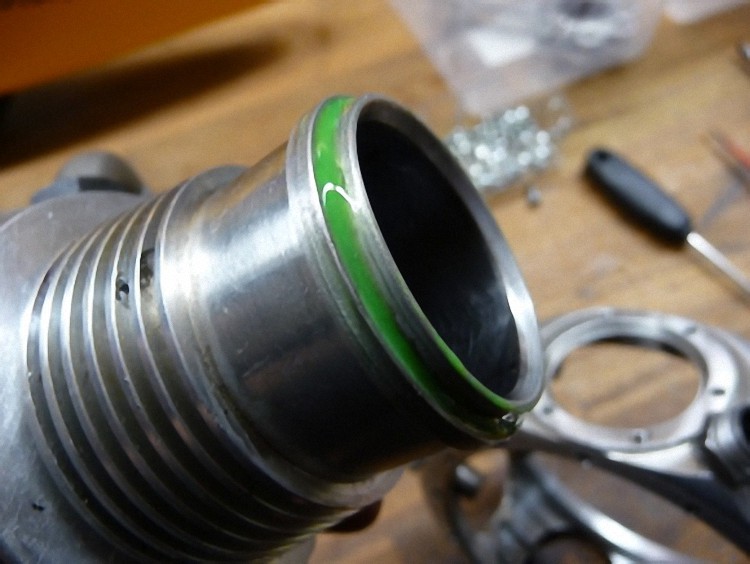
Eine Faustformel lautet: Die Tiefe eines Schrauben-Bohrloches sollte immer das 2-fache des Durchmessers der Schraube (bei M4 = min. 8 mm tief) betragen. Auch eine richtige Zylinder-Abdichtung ist sehr wichtig. Je dichter der Motor ist, um so besser springt er an und behält ein niedriges und sicheres Standgas.
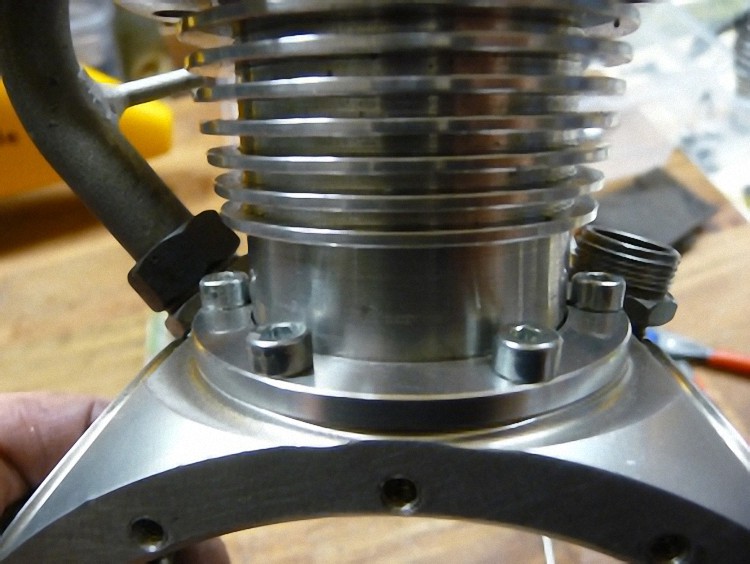
Ich verwende ausschließlich Schrauben der Festigkeit 8.8 und Oberfläche feinverzinkt. Die Montage geht zügig voran.
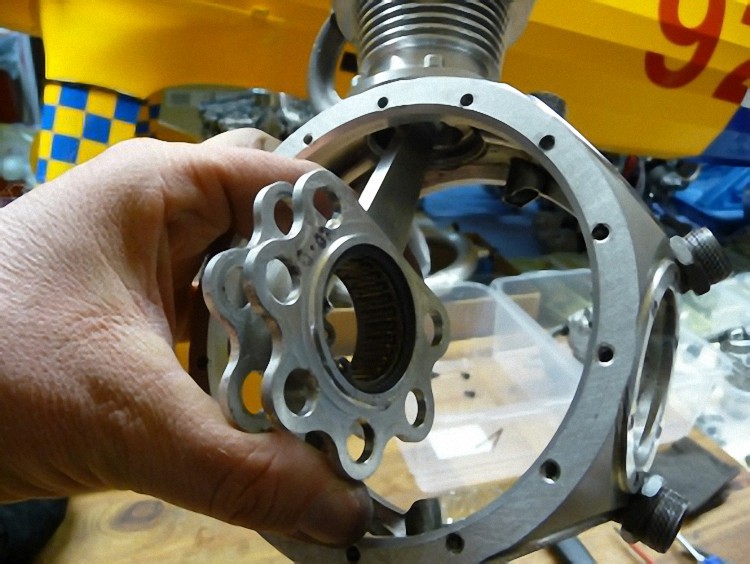
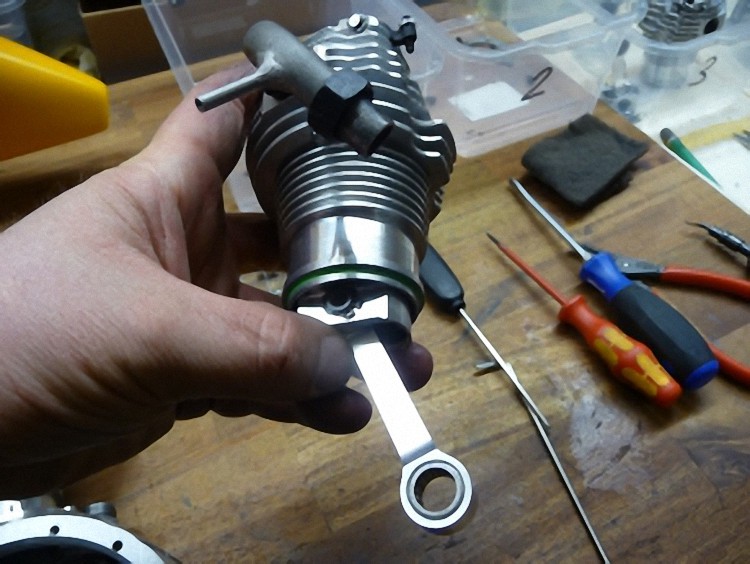
Die Kolben mit dem Pleuel werden nun in den Zylinder eingeschoben und die einzelnen Zylinder nacheinander verschraubt.
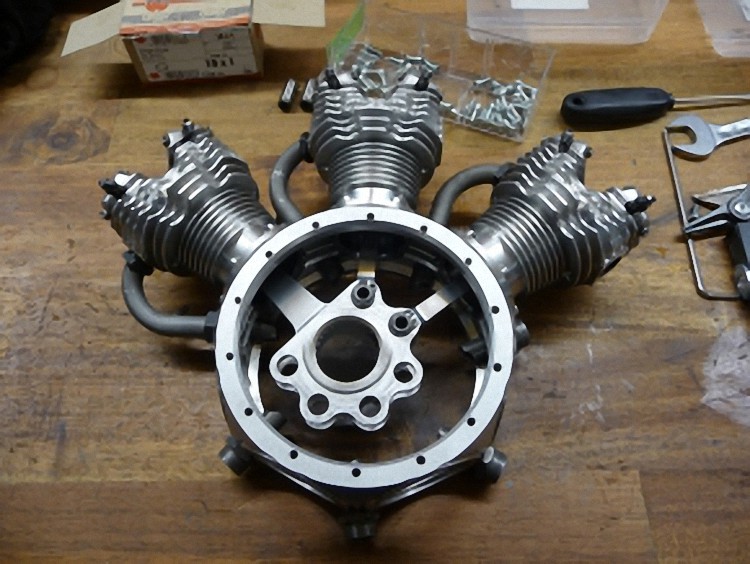
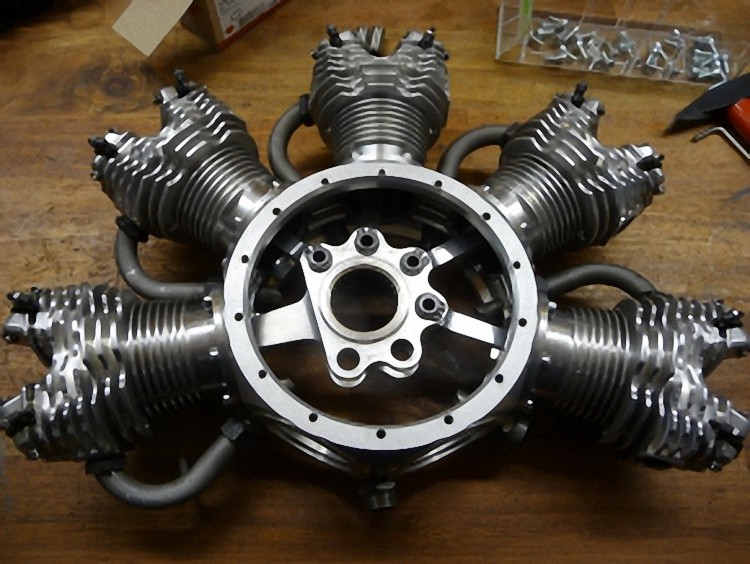
Die Nebenpleuel müssen jetzt mittels einem Pleuelbolzen in das Mutterpleuel eingehangen und gesichert werden.
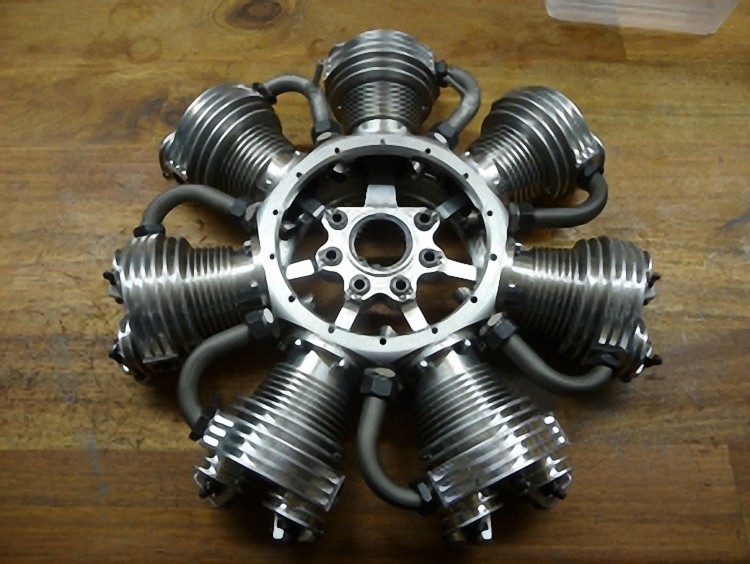
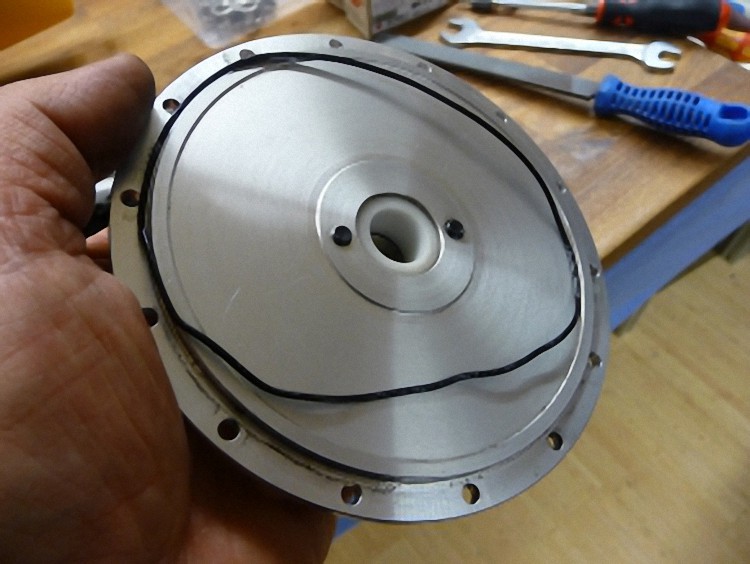
Bei der Heckplatte habe ich den Original O-Ring entsorgt und durch Flächendichtmasse ersetzt. O-Ringe setzen sich mit der Zeit und werden spröde = keine Abdichtung. Motor zieht Falschluft.
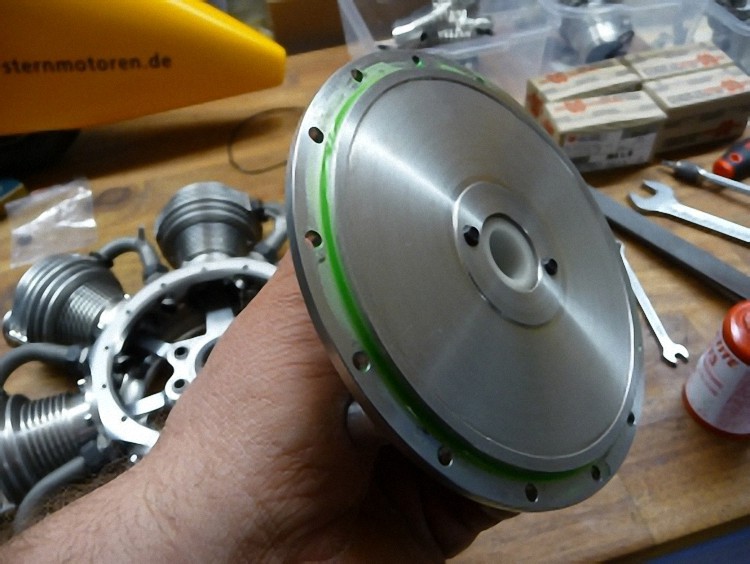
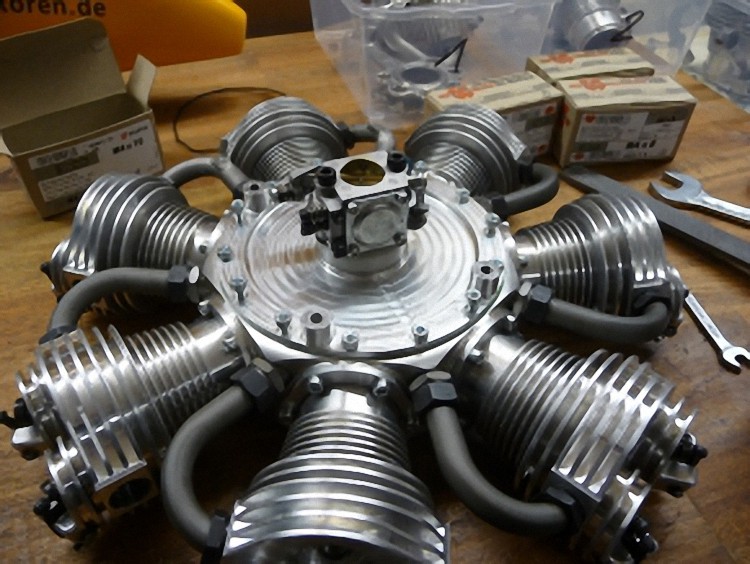
Neue Schläuche für den Vergaserimpuls werden eingezogen. Mit einem neuen Y-Stück als Verteiler. Die Schläuche sind spritresistent und härten nicht aus. Anders als die Originalen.
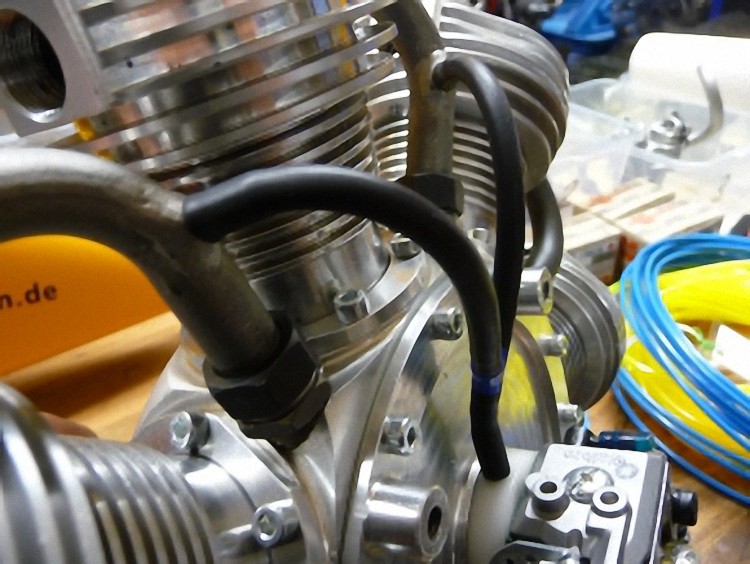
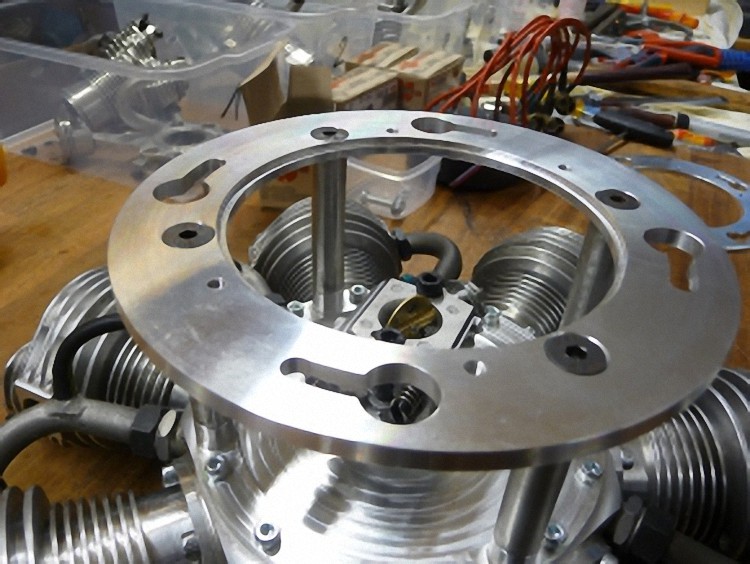
Montage Motorträger
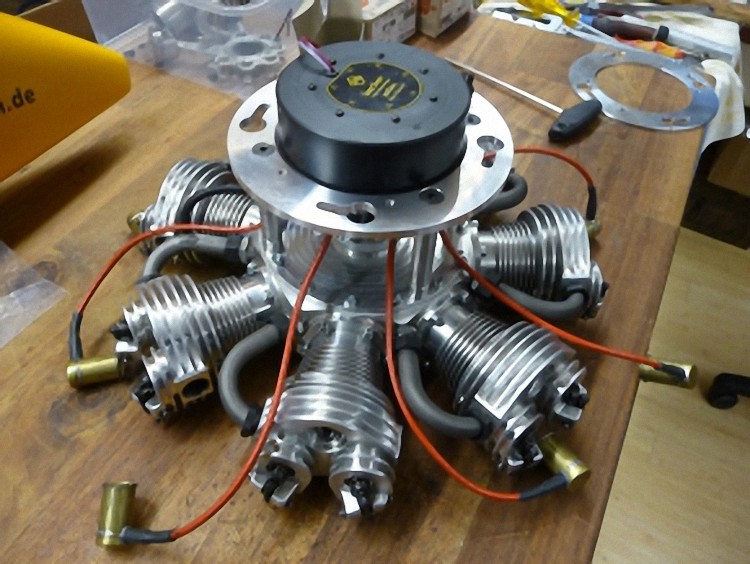
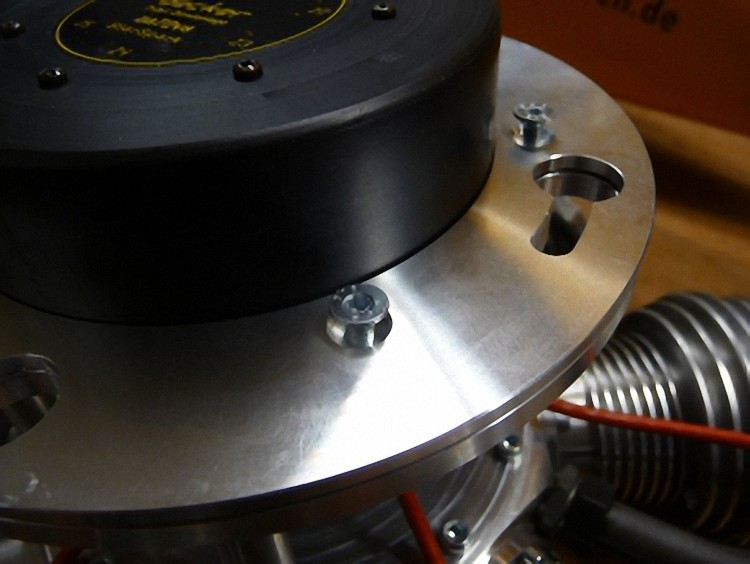
Mittels Adapterplatte wird die Becker-Zündung sauber im Motorträger fixiert.

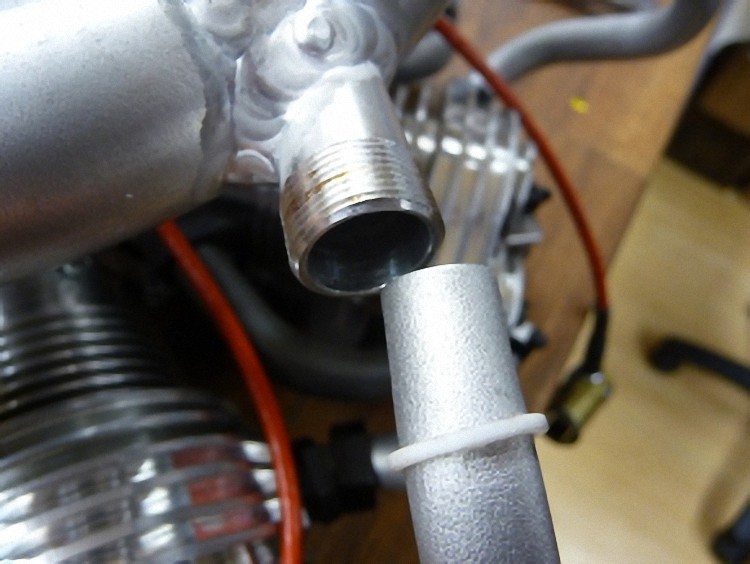
Der Ringschalldämpfer wurde ab Werk nicht montiert, sondern nur beigelegt. Aus gutem Grund. Er passt überhaupt nicht! Über die Jahre habe ich einige RSD montiert und einiges erlebt, aber so etwas lieblos gebogenes ist mir wirklich noch nie untergekommen.

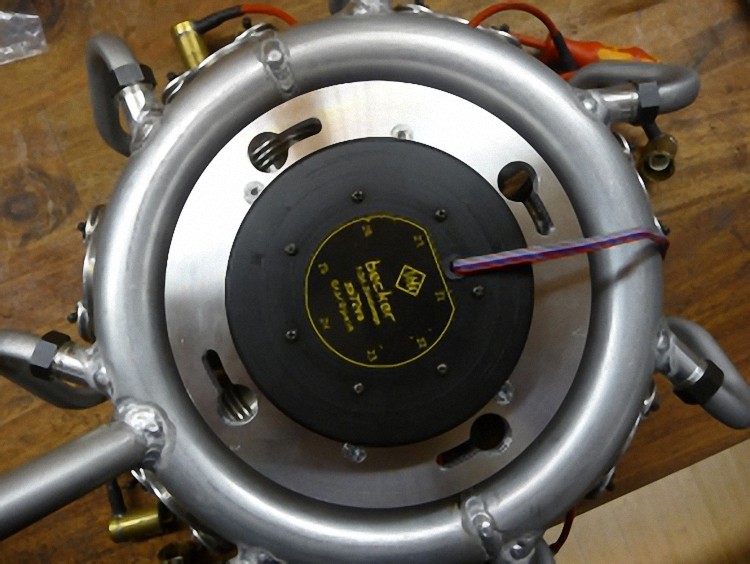
Da der Ringschalldämpfer so gut wie Spannungsfrei montiert werden muss und mittig zur Motorträger-Platte sitzen soll, habe ich alle Aluminiumkrümmer in akribischer Nacharbeit nachgebogen. Auch die Schweißstutzen habe ich mittels Wärmebehandlung justiert.
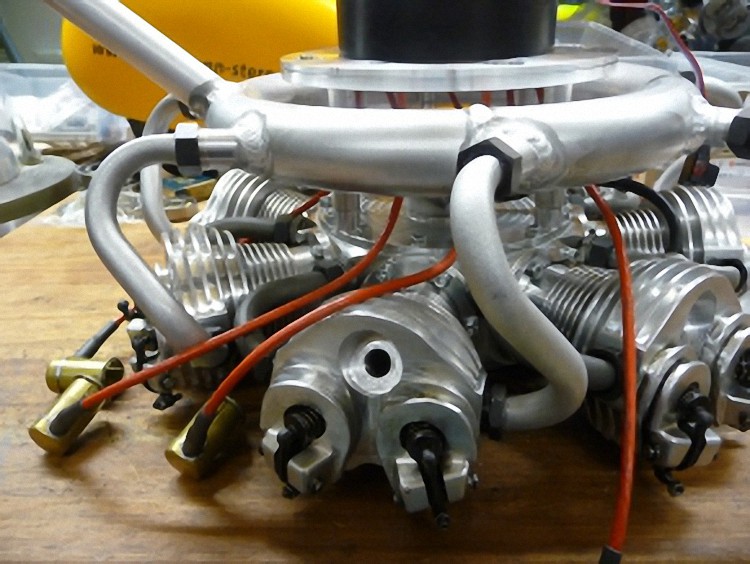
Nach endlosem Fluchen und Stunden später sitzt der Dämpfer endlich da wo er hin soll und sieht sehr gut aus.
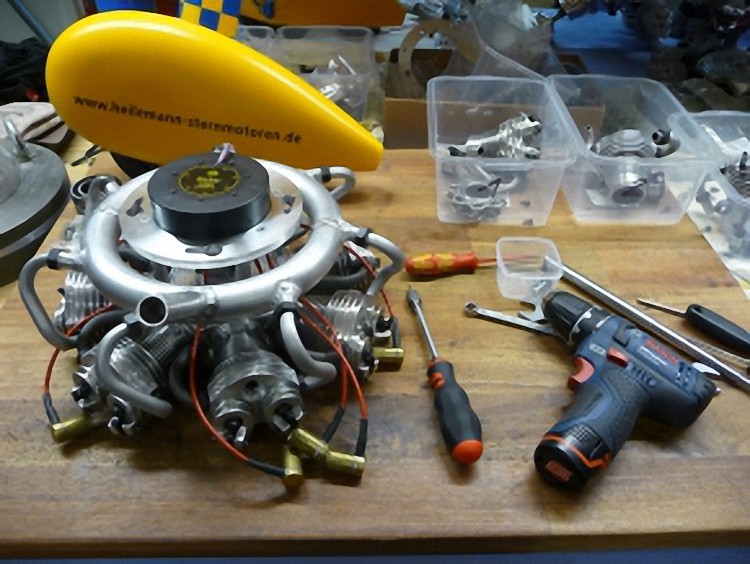
Und jetzt zum Nockengehäuse. Es wurde abgedreht um den Namen und das Logo der Firma Seidel und die Hammerschläge und Kratzer zu entfernen (neuer Motor?).
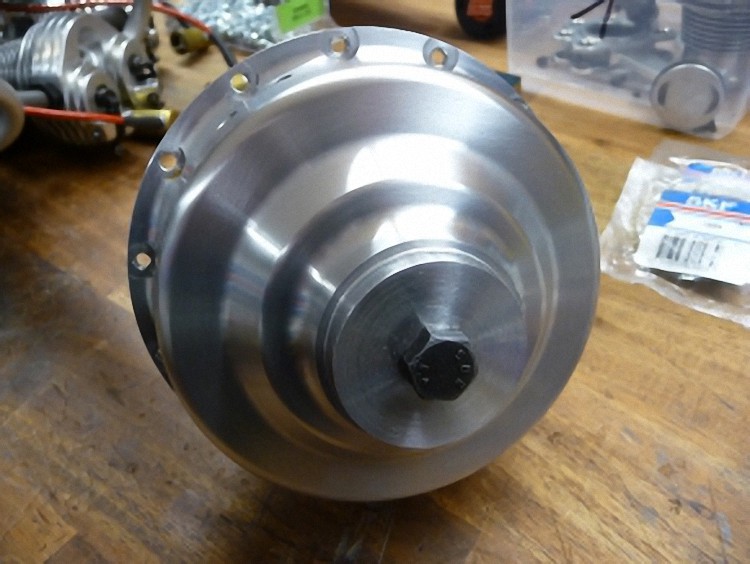
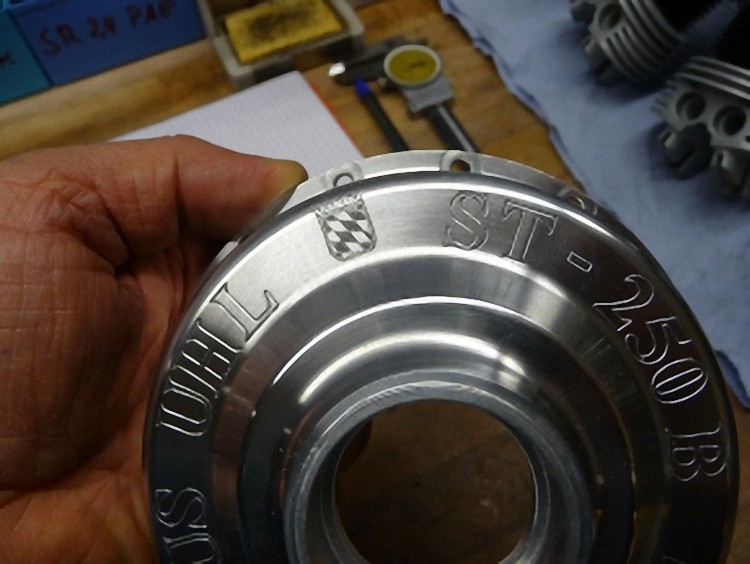
Auf Wunsch von Klaus Uhl wurden; sein Name, das Bayerische Wappen sowie die Motordaten, von unserer Graveurin in akribischer Handarbeit, eingraviert und von mir auf Hochglanz poliert.
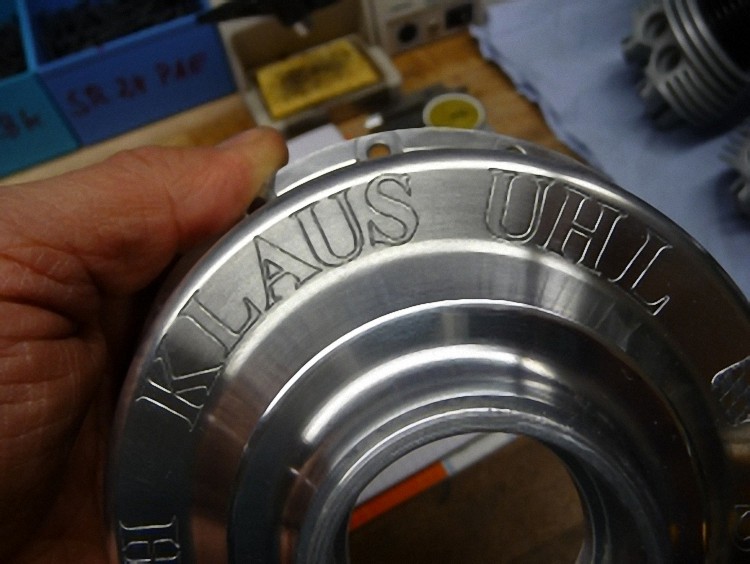

Die indischen Lager habe ich kurzer Hand durch europäische Lager ersetzt.


Das gleiche auch bei der Hauptlagerscheibe, die die Kurbelwelle aufnimmt.


Und bei der Nockenscheibe das gleiche. Zu dem habe ich das Lager eingeklebt, da es keinerlei Sicherung hat (durch einen Bund oder Sicherungsring).
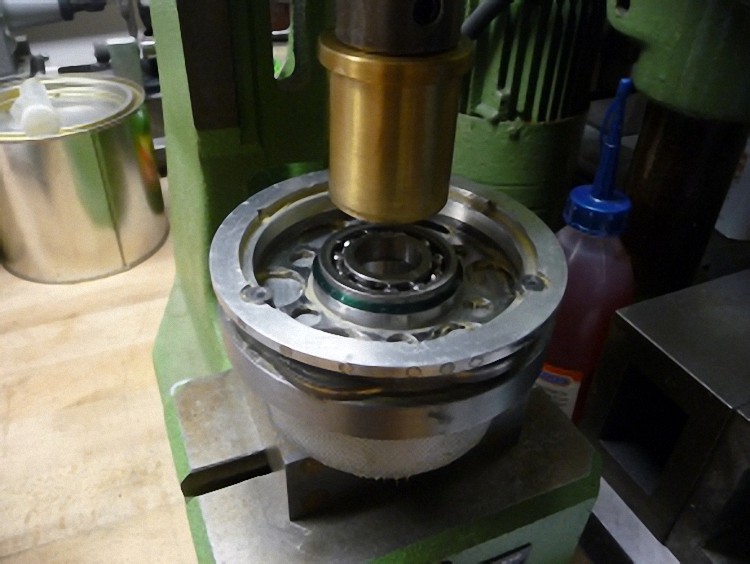

Nocke wird in das Nockengehäuse eingebaut, mit einer anständigen Fettfüllung die über Jahr ausreichend ist.

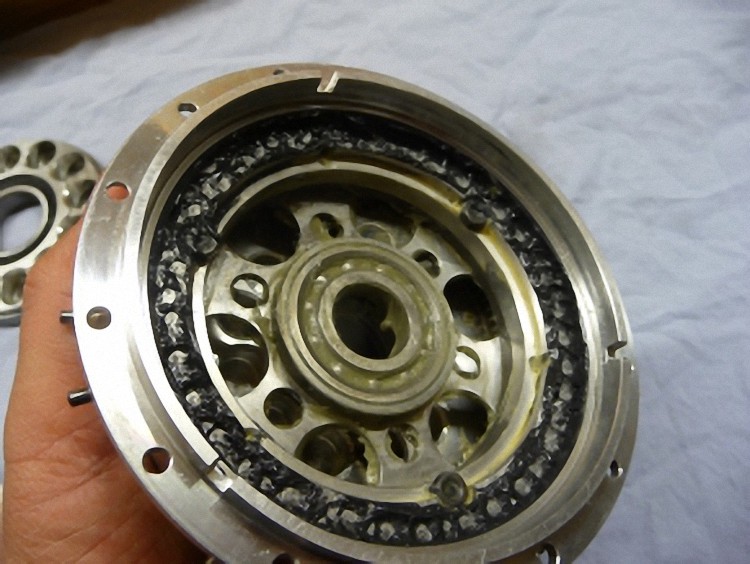
Die Kurbelwellenverzahlung habe ich auch mit Fett versehen und nach Justierung der Steuerzeiten, mittels Gradscheibe (360°) und Zündkästchen (zur Kontrolle) in das Nockengehäuse eingepresst.
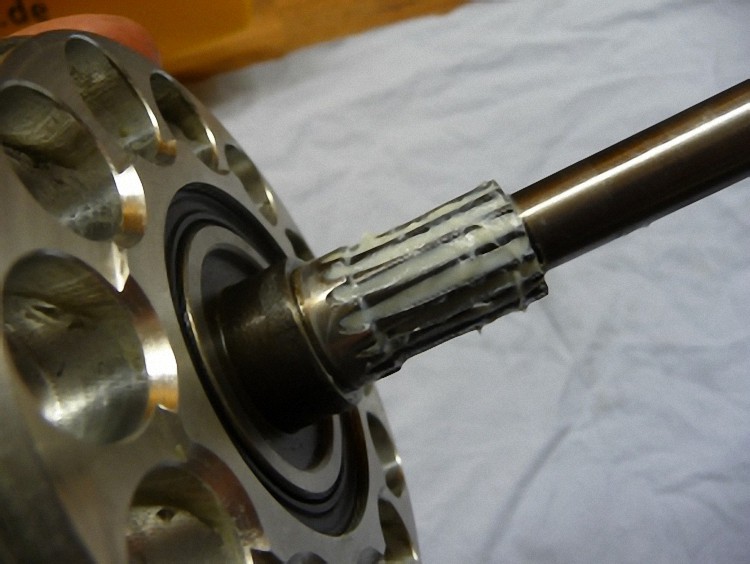
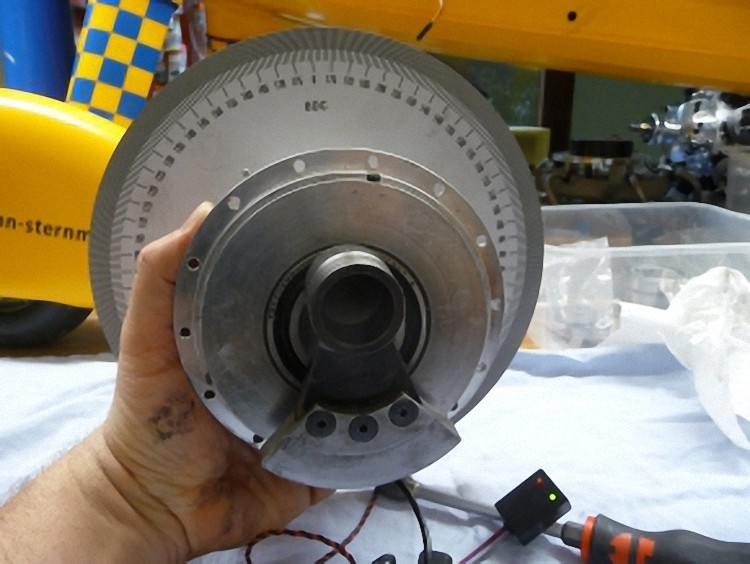
Kontrolle mit Gradscheibe und Einpressen der Kurbelwelle.
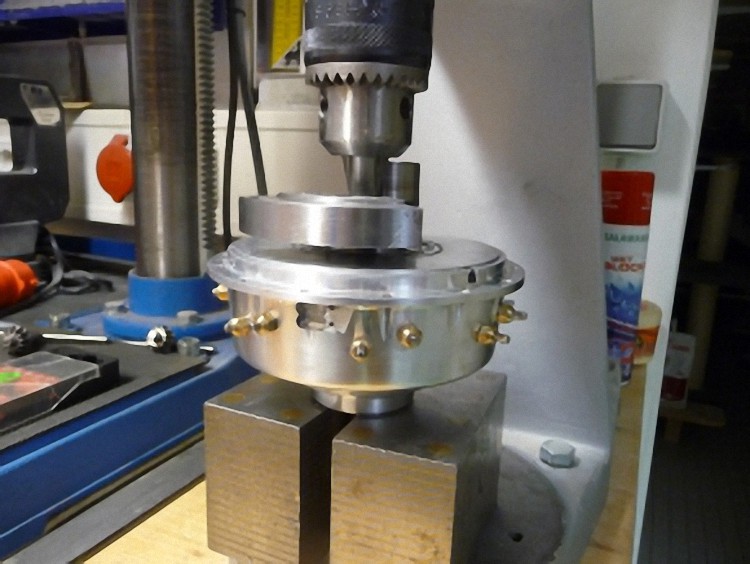
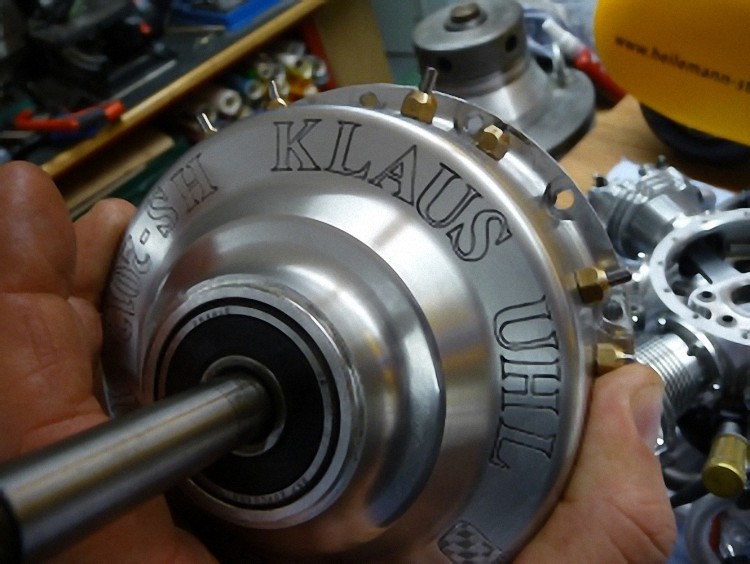
Damit die Gravur des Nockengehäuses noch besser zur Geltung kommt habe ich sie schwarz gefüllt und nachpoliert.

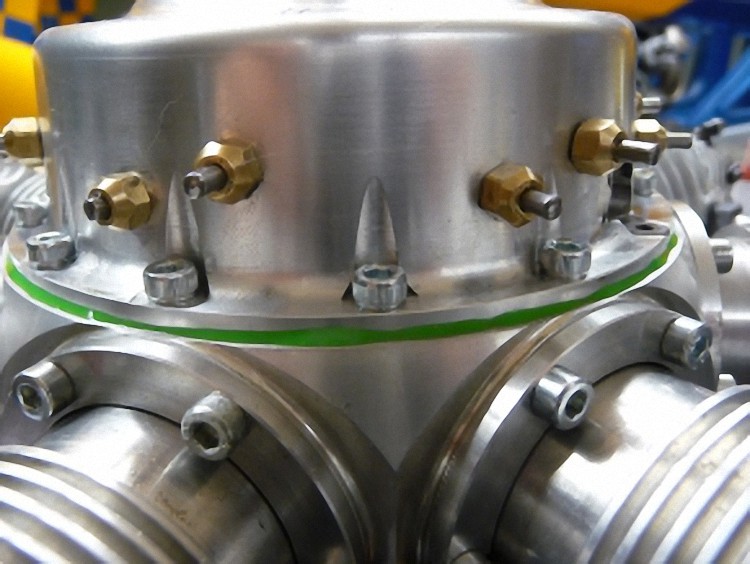
Das Nockengehäuse wird mit dem Motorgehäuse verschraubt und der Motor ist fast fertig.


Bei den Original Stösselstangen ist eine deutliche Stauchung zu sehen. Deshalb habe ich die Einsätze ausgepresst ...
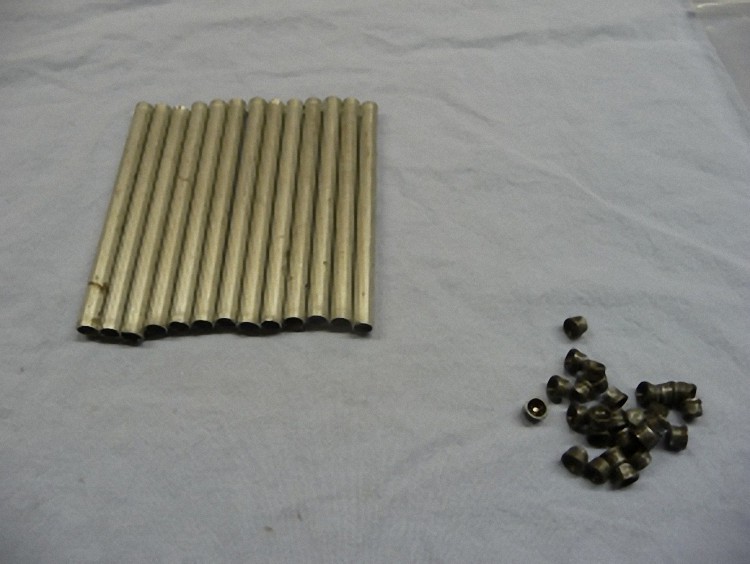
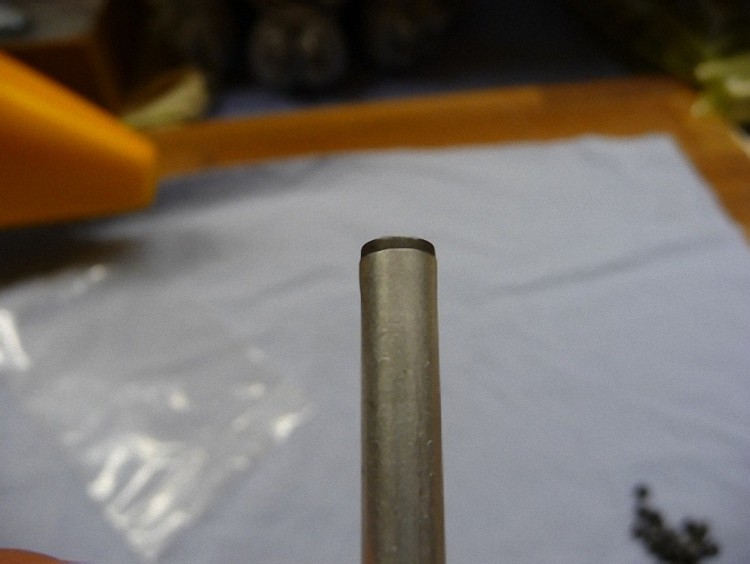
... und in die neuen Rohre eingepresst. Anschließend gut gefettet und montiert.
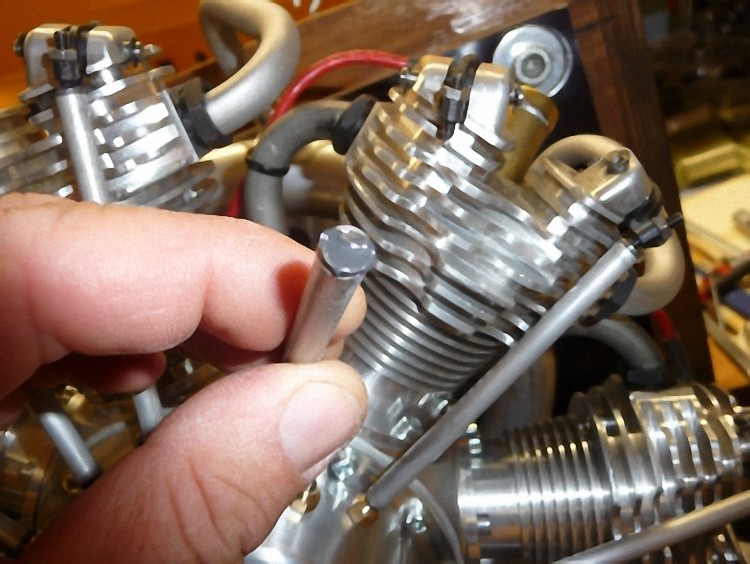
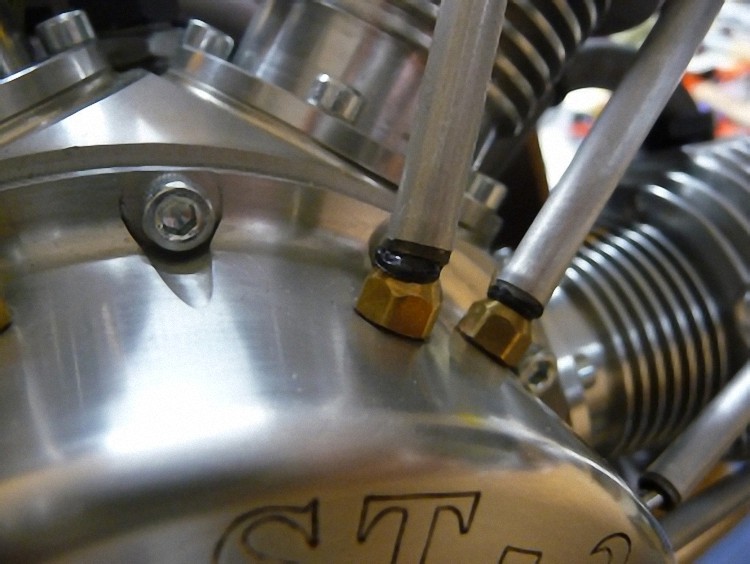
Jetzt werden die Ventile eingestellt. D.h. den leichten Höhenschlag der Nocke ermitteln, in diesem Fall 0,15 mm und die Ventile auf 0,1 mm eingestellt.
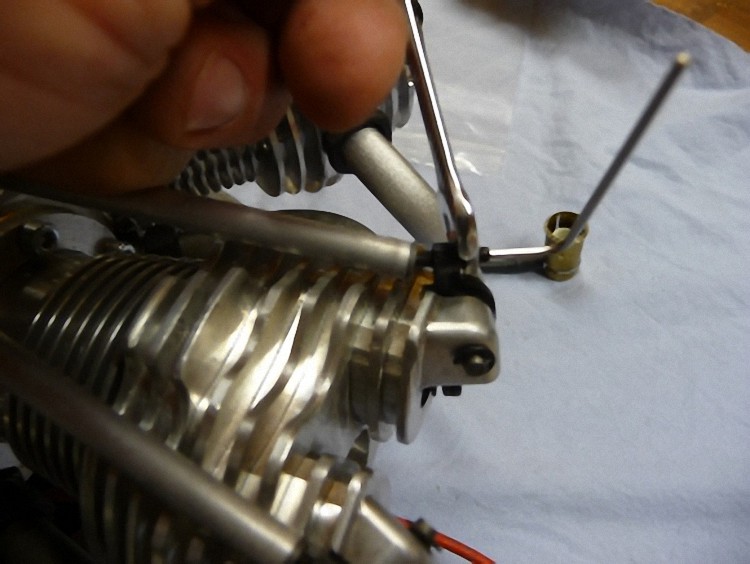

Die Zündkerzen habe ich auf Spaltmaß 0,4 mm geprüft und teilweise nachgebogen.
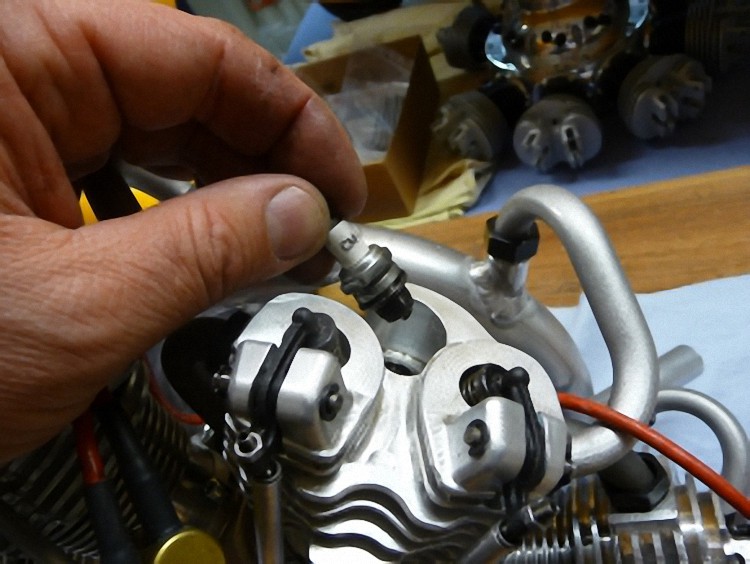
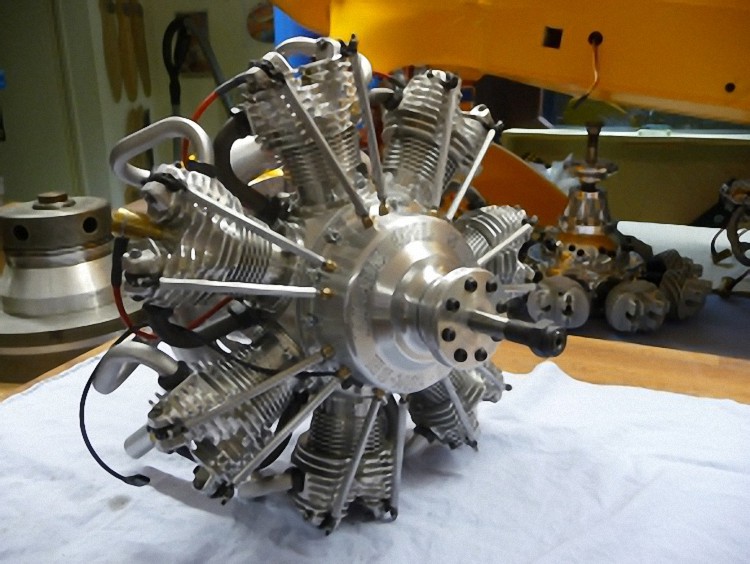
Zündkabel noch sauber verlegen und auf Prüfstand montieren.
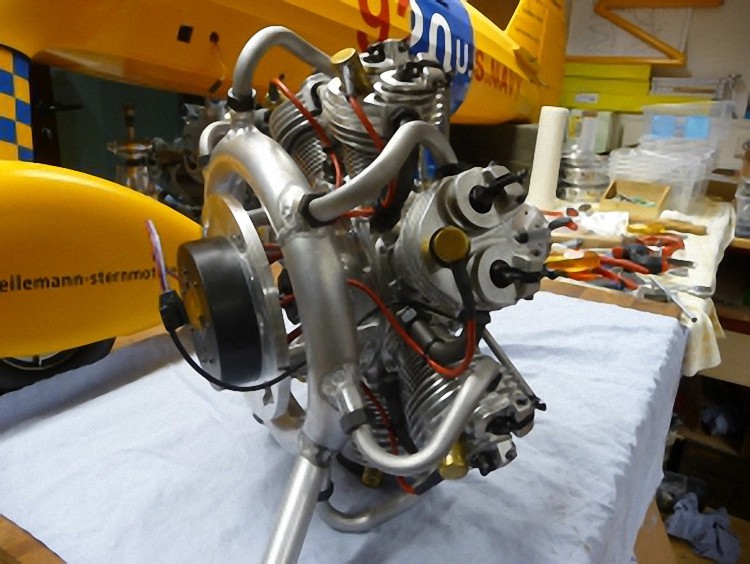
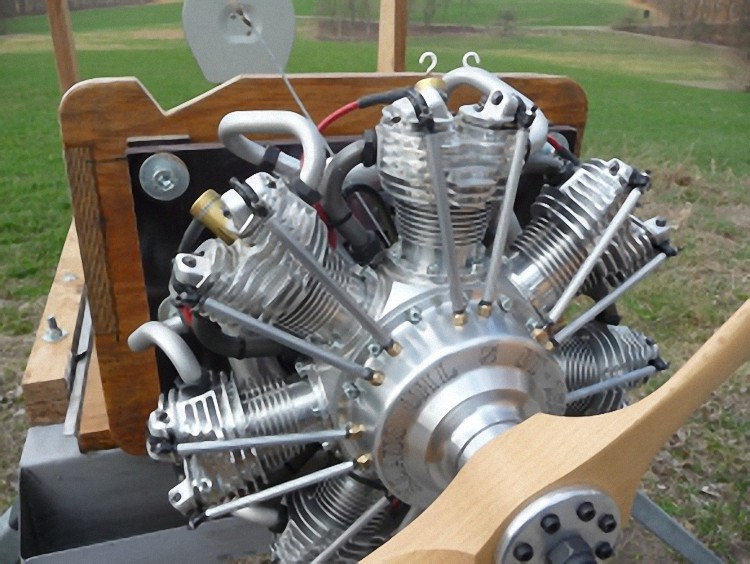
ES IST GESCHAFFT
Der Motor springt sehr gut an, läuft sauber durch und hat ein niedriges und stabiles Standgas.
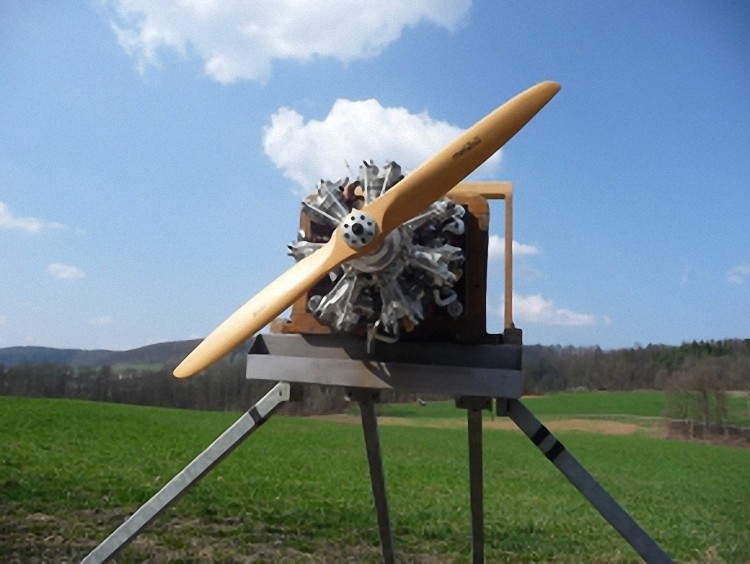
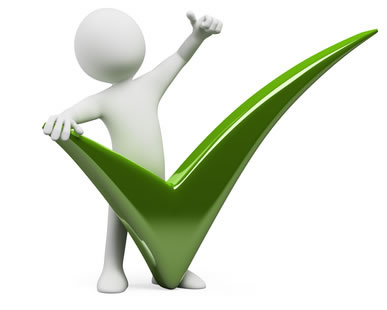
Jetzt kann Klaus Uhl nach viermonatiger Umbauzeit seinen Motor wieder in Empfang nehmen.
Wir freuen uns schon jetzt, den Motor hoffentlich beim nächsten Sternmotorentreffen in seiner GeeBee fliegen zu sehen.
Einen herzlichen Dank geht auch, wie immer, an die helfenden Hände im Hintergrund: Peter Haag, Florian Karpf, Carmen Kugler und meine Frau Elke.
Ohne Euch wäre es nicht möglich solche Projekte umzusetzen.
E-Anlasser für Sternmotor
Meinen 18 Zylinder Doppelstern mit 700 ccm werde ich mit diesem E-Anlasser ausstatten.

Elektromotor mit angeflanschtem Planetengetriebe
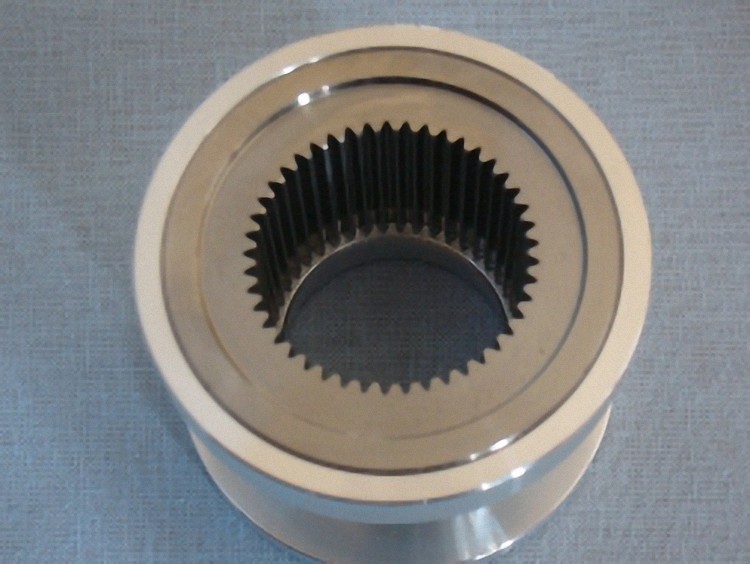
Zahnkranz eingepresst
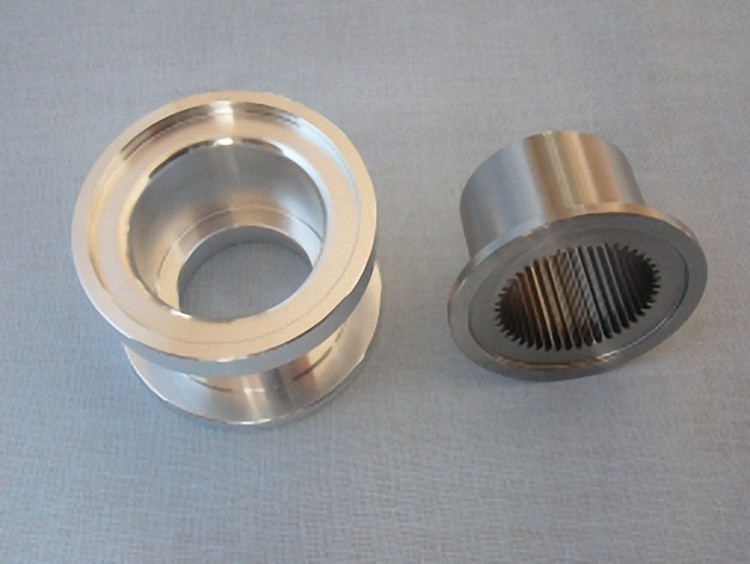
Aluminiumgehäuse und Zahnkranz

Dreistufiges Planetengetriebe in Einzelteilen
Neuer Bauabschnitt:
Zuerst wollte ich mit dem Anlasser direkt auf die Kurbelwelle und den Vergaser aus der Mitte setzen. Es hat sich jedoch gezeigt, dass der Vergaser mittig platziert, die bessere Wahl ist. Also wurde noch ein Zwischenzahnrad angefertigt (mit Freilauf). Daraufhin wurde das dreistufige Planetengetrieb auf zwei Stufen reduziert. Die Anlasserwelle sitzt nun aus der Mitte und macht Platz für den Vergaser.
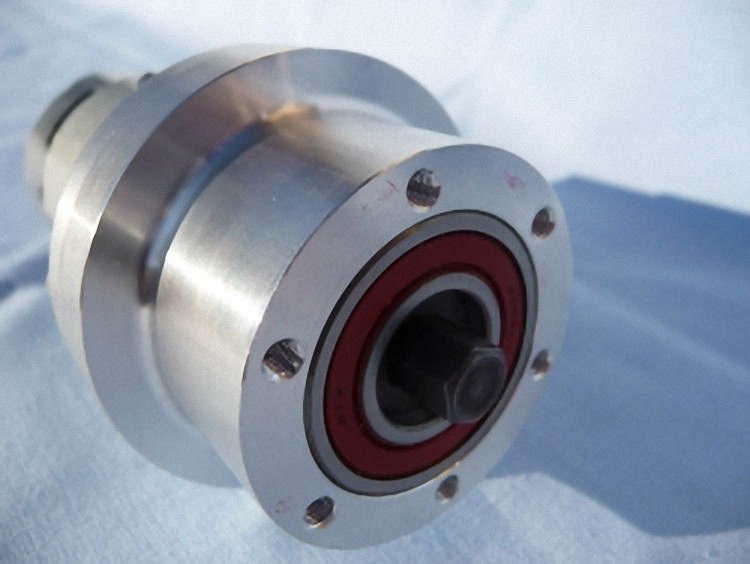
Neues zweistufiges Planetengetriebe mit E-Motor montiert
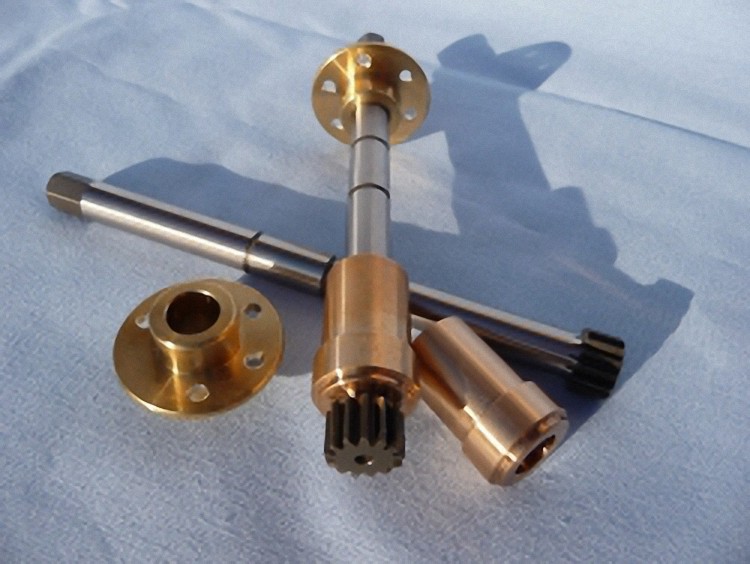
Anlasserwelle mit hinterer/vorderer Lagerung (rot = Lagerbronze / gelb = Messing)
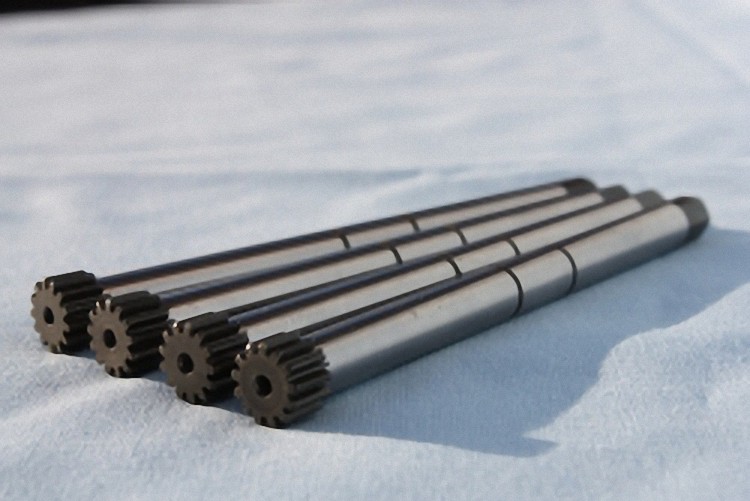
Einsatzgehärtete und geschliffene Anlasserwellen
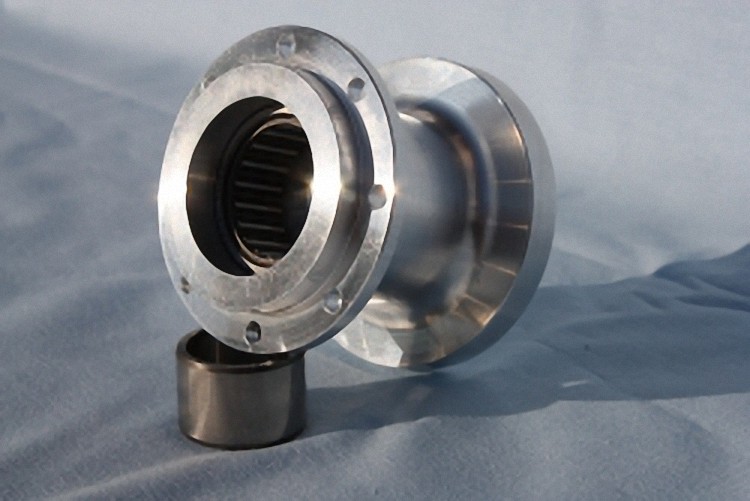
Hauptlagerung für Kurbelwellenmitnehmer
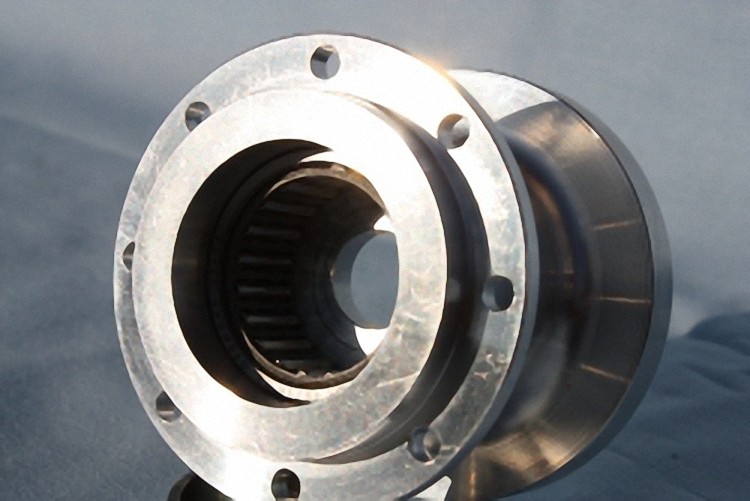
eingeschrumpftes Nadellager für Kurbelwellenmitnehmer
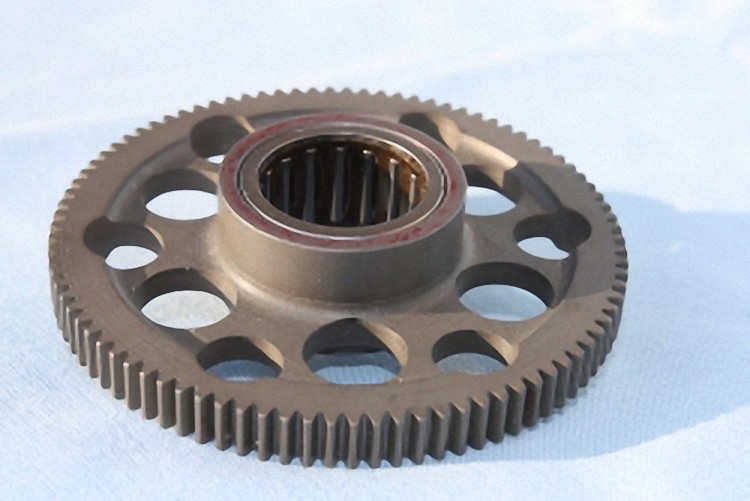
Einsatzgehärtetes Übersetzungszahnrad mit geschliffenem Lagersitz für Freilauflager
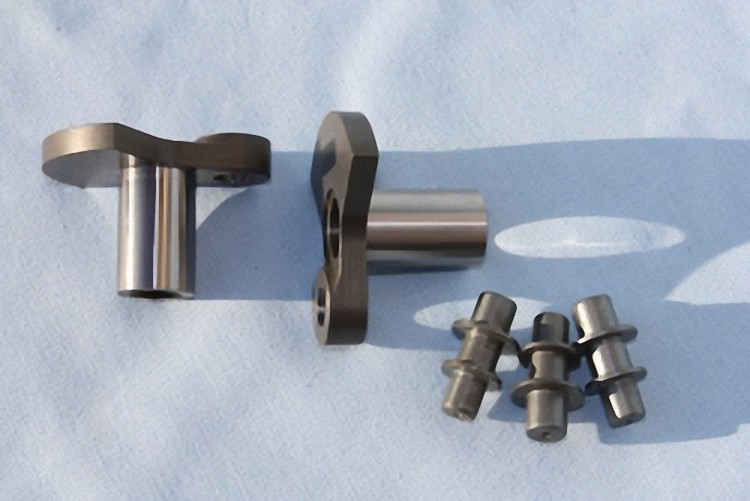
Kurbelwellenmitnehmer und Mitnehmerzapfen
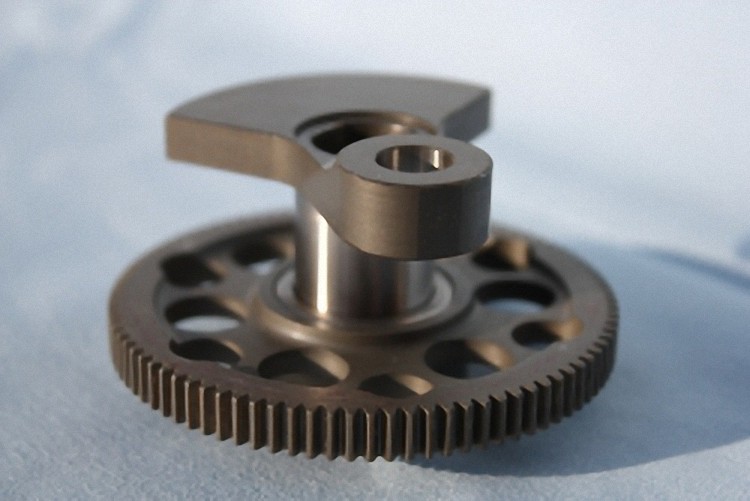
Zahnrad mit eingepresstem Freilauf mit Kurbelwellenmitnehmer
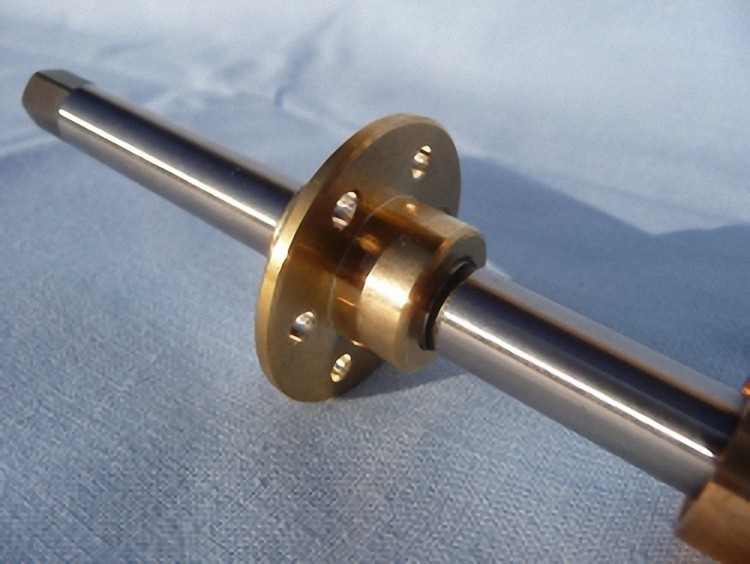
hintere Lagerstütze für Anlasserwelle
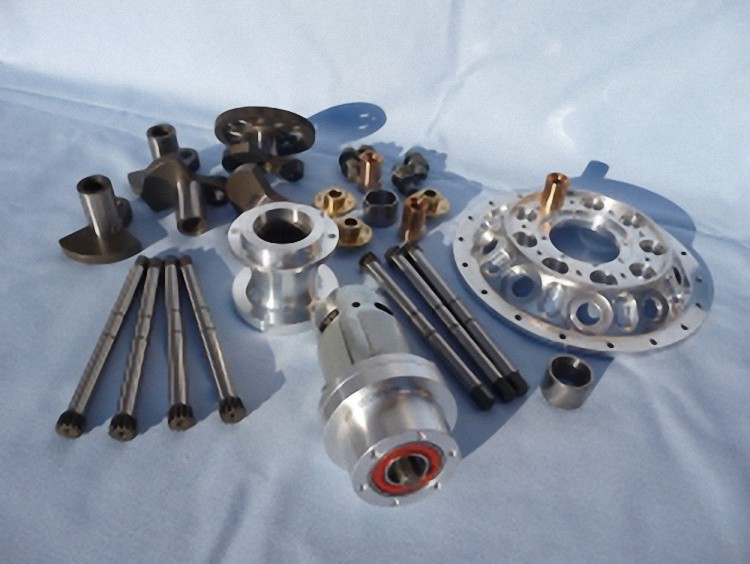
fast alle Einzelteile komplett
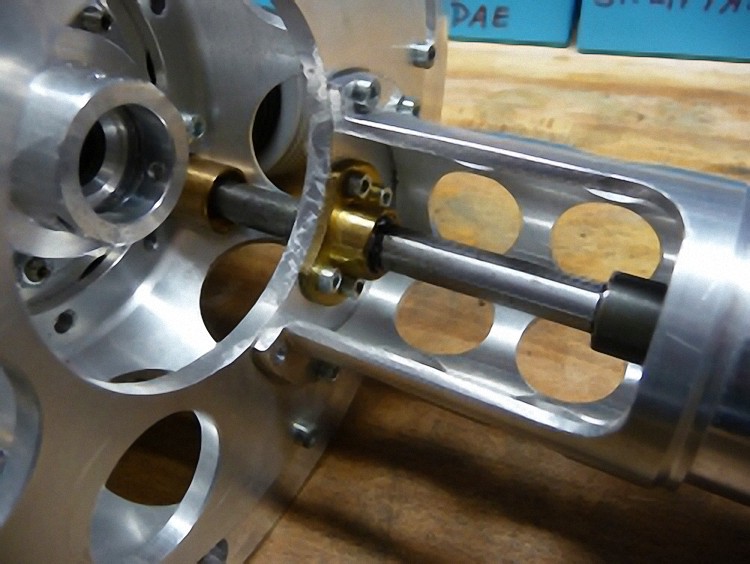
Anlasserdom mit eingebauter Welle
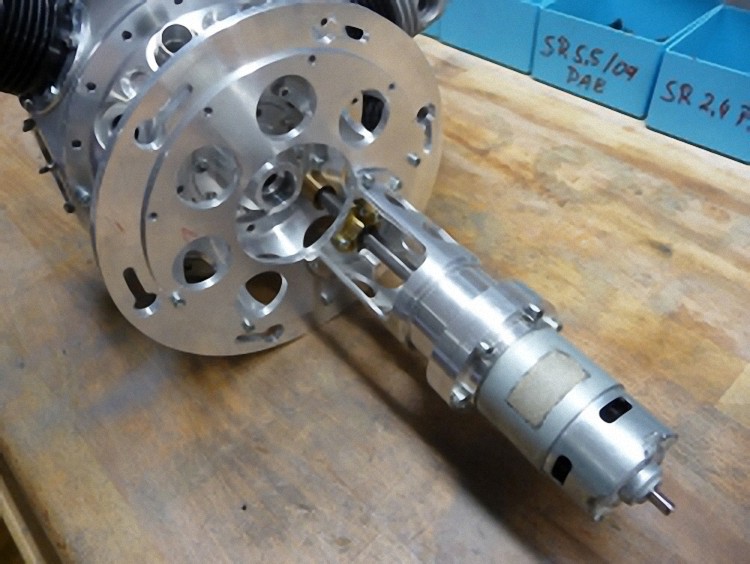
Anlasser komplett angebaut